- Home
- Blog
- Production & Lab
- 4 Tips for Choosing A Silicone Rubber Suppliers
4 Tips for Choosing A Silicone Rubber Suppliers
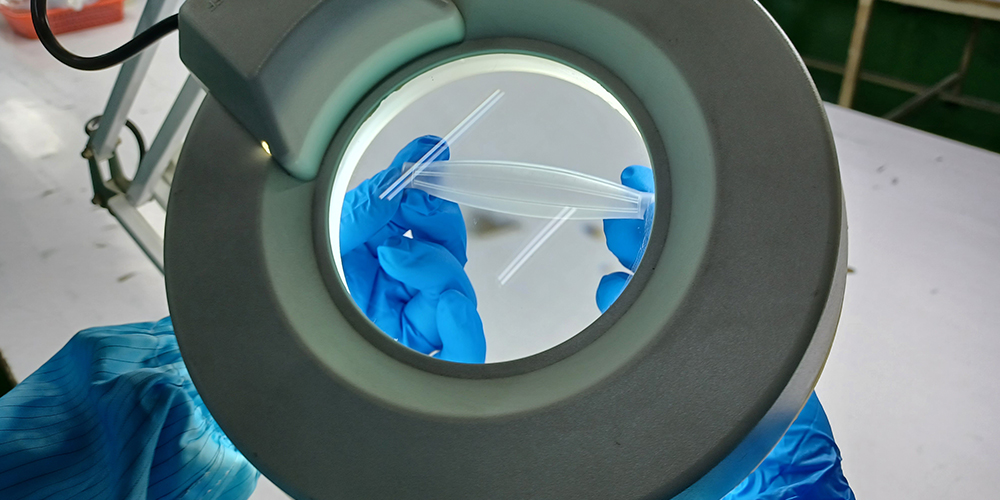
As the advantages of silicone rubber products are seen by more and more people, from daily necessities to high-precision industries such as optical parts, medical equipment, auto parts, etc., all rely on silicone raw materials. Many NR/Black Rubber-based factories and even non-related industries have transformed into this field one after another. The number of silicone rubber factories in the market continues to rise every year. Whether it is a franchise or a dual-purpose nature, customers have more choices. For factories, a fierce competition is inevitable. In this case, for customers who have a need for silicone product development, how to choose the most sophisticated and suitable silicone factory from the vast sea? Before giving the four practical silicone factory identification points, it is necessary to understand silicone Only by knowing the relevant characteristics and manufacturing processes can we accurately choose one out of ten thousand, and find a pleasant manufacturer partner.
What Is Silicone Rubber?
Silicone rubber is a material positioned between synthetic rubber and synthetic plastic polymers, widely used in industries and daily items due to its unique elasticity, resistance to extreme temperatures, and oxidation resistance. Recognized as a safe and sustainable material, silicone is known for its non-toxic, eco-friendly properties and high transparency, making it ideal for use in medical devices, kitchenware, and protective cases for electronics. Furthermore, silicone's excellent sealing capability makes it a preferred material for sealants and gaskets. For environmentally conscious consumers, its durability and reusability greatly reduce resource waste, driving its growth as an ideal choice across various industries. Silicone is now a premium material that combines performance with environmental value.
〈Extension Reading: What You Should Know About Silicone Rubber?〉
〈Extension Reading: Is Silicone Rubber Better Than Rubber?〉
Types and Silicone Rubber Molding Methods?
Solid Silicone(HTV or High Consistency Rubber, HCR)
The appearance is translucent and solidified. It is usually called a raw meal before the mixing process. For example, the hardness and color required by the finished product conditions are all prepared during the mixing process. It is also the most commonly used raw material type.
Molding Method:
Divide the mixed raw material semi-finished products into equal parts according to the product structure, size, and weight (just like dividing the dough into small pieces in the preparatory work of bread), and then place the silicone semi-finished products in the molds that open and close one by one, and heat them. Finished product molding.
Feature:
The above-mentioned molding method is called the compression/hot pressing molding process, which is the most common and mature manufacturing process in the market, and the production cost is also relatively cheap.
〈Extended reading:What is Solid Silicone HTV〉
liquid silicone(LSR)
The appearance is highly transparent and liquid, and the raw materials do not need to be mixed. This is why liquid silicone rubber can keep the raw materials clean and free of impurities compared with solid silicone rubber (due to less impact from the external environment).
Molding Method:
Directly place the barreled A/B liquid silicone raw material on the liquid injection machine feeding place, and the automatic equipment will start accurate feeding according to the product specifications and conditions to complete the injection of the product.
Feature:
The purpose of the liquid silicone injection process is to meet the requirements of high-precision products (such as strict burr control) or high-transparency appearance (such as medical-grade human contact products), etc., so the cost is relatively high, and the application is not as common as solid silicone molding.
〈Extension Reading: How is silicone rubber molded?〉
〈Extended reading:How liquid silicone rubber work on your demands?〉
3 Common Processing Techniques Used in Silicone Rubber Suppliers
The production of silicone products involves a range of processing techniques, each of which affects the product's quality, appearance, and cost. Below are several common techniques employed in silicone manufacturing:
〈Extension Reading: How is silicone rubber molded? 〉
1. Liquid Silicone Injection Molding
Silicone injection molding is a fast and precise production method ideal for creating high-quality silicone products with intricate details. This technique includes single-material injection, embedded molding, and two-material injection types. The process starts by injecting liquid silicone into a mold, where it is shaped under high pressure. This method ensures the product's precision, dimensions, and thickness, making it suitable for various applications. Different injection types can be selected based on the intended product use, allowing for the production of durable silicone products with complex shapes.
〈Extension Reading: All Types and Applications of Silicone Injection Molding〉
2. Solid Silicone Compression Molding
Solid silicone compression molding involves placing solid silicone material into a preheated mold. By applying high pressure to the silicone, it fills every detail of the mold. Then, high temperatures vulcanize the silicone, causing it to solidify and take shape. Due to the properties of solid silicone and the high temperature and pressure in the compression molding process, this method is particularly suitable for producing simpler silicone products that do not require high precision or complex shapes. Compared to liquid silicone injection molding, solid silicone compression molding is simpler and more cost-effective, making it widely used in various consumer goods and industrial parts. However, due to the limitations of solid silicone, compression molding is less capable of achieving the same level of detail and complexity as liquid injection molding.
〈Extension Reading: Liquid Injection Molding (LIM) VS Compression Molding; what fits you best?〉
3. Silicone Extrusion Molding
Silicone extrusion molding involves placing solid or liquid silicone material into an extruder, where it is shaped by heating and applying high pressure. The shape of the extruder head determines the cross-section of the final product, allowing for the production of various silicone products, such as silicone tubes and strips. Compared to compression molding, extrusion molding is more suitable for producing long, continuous shapes or products with specific cross-sectional shapes. As extrusion molding is a continuous production process, it is also more efficient. However, extrusion molding is less suitable for producing complex shapes, and controlling the product's thickness is more challenging.
Common Applications of Silicone Rubber
Whether it is solid or liquid raw materials, silicone rubber has a considerable share in various fields and has become an indispensable raw material. Therefore, when the cost of international silicon raw materials rose sharply, countless industries were hit, which shows the impact of silicone raw materials. force.
Automotive
Silicone's resistance to high temperatures, compressibility, and acid-alkali tolerance make it widely applicable in automotive manufacturing and interior parts. High temperatures are common during automotive production and operation, and silicone’s thermal range (-50ºC to 200ºC) allows it to withstand these extreme conditions near engines and various electronic components. Its excellent compressibility provides long-lasting sealing, preventing chemical leaks and protecting power connections. Additionally, silicone's resistance to UV rays and chemicals makes it durable under prolonged exposure, so it is widely used in car interiors, such as display screens, control panels, and steering wheel controllers, enhancing convenience, aesthetics, and durability.
〈Application: Versatile applications in the Automotive industry 〉
〈Recommendation: Rubber Seals / Gaskets〉
Medical & Healthcare
Silicone holds a critical place in healthcare, found in diagnostic equipment housings, implants, and devices directly in contact with the human body. Medical-grade silicone’s wide use stems from its superior biocompatibility, high transparency, and non-toxicity. It is non-irritating, unlikely to trigger allergies or rejection, making it suitable for high-standard medical products. The clarity of liquid silicone also provides a clean, hygienic appearance, ideal for products like baby bottle nipples and diving masks. These properties make silicone an ideal choice in the medical field, meeting stringent safety and stability requirements.
〈Extension Reading: Medical Grade Silicone: How to define it? 〉
〈Application: Silicone Rubber in Medical & Healthcare Application 〉
〈Recommendation: Biocompatibility LSR〉
Consumer Goods
Silicone is pervasive in consumer goods, from smartwatch bands to phone cases. Its flexibility, durability, and eco-friendliness enhance electronic products by providing a comfortable user experience. Silicone's excellent waterproofing allows electronics to adapt to various environments, while its insulating properties protect electronic components' safe operation. The soft, skin-friendly feel of silicone also improves human-centered design in everyday items, from phone cases to earbud covers and button surfaces, delivering a superior user experience. Silicone applications enhance the durability of electronics and consumer goods while aligning with modern demands for eco-friendliness and health-consciousness.
〈Extension Reading: How to distinguish food-grade silicone and regular silicone 〉
〈Application: Life Without Silicone Rubber? No way! 〉
〈Recommendation: Over-molding keypad〉
Industrial Device
Silicone’s excellent thermal conductivity, insulation, and abrasion resistance make it ideal for parts in precision instruments and equipment. From caliper buttons to industrial O-rings, silicone is widely used, especially for its durability against extreme temperatures, chemical corrosion, and aging. For example, in chemical factories, silicone seals prevent chemical leaks, while outdoor equipment made of silicone withstands weather elements, ensuring reliable operation. These properties not only improve industrial productivity but also contribute to green manufacturing. With increasing environmental standards in industries, silicone is a promising, eco-friendly material with vast potential for growth.
〈Extension Reading: What is silicone zebra connector and how they made? 〉
〈Application: The small part with a big role 〉
〈Recommendation: Silicone Zebra Connector〉
4 Tips for Choosing A Silicone Rubber Suppliers
Since silicone rubber parts are often only one of the components of the product in the supply chain, at the beginning of product design, the designer may not be proficient in the physical properties of silicone rubber. It is relatively uncontrollable, so most of the entrusted customers rely on the evaluation and advice of the silicone rubber factories to ensure that the product can be finally formed and can meet the operation requirements of the whole machine. At this time, it is very important to find a professional and careful silicone factory to check the whole process from development to production. It is not easy to select a good silicone factory that can cooperate for a long time. The following 4 core characteristics will help you find what you are looking for!
High reputable manufacturer
Reputable silicone rubber factories can often provide good product quality, responsible service attitude, product prices are more in line with market conditions, no malicious irrigation, no price cut competition, stable delivery, and other advantages, so as to have a certain reputation, and These advantages can bring quite substantial help to customers. Generally, such high-quality silicone factories rely on word-of-mouth or peer-to-peer referrals, and it is more difficult to search through unfamiliar markets. And this kind of unobtrusive core value is also difficult to see from the Internet or e-commerce platforms. It is necessary to actually cooperate and observe carefully in order to gain a deep understanding.
Professional and technical team
A professional and technical team should consider the background of the silicone factory. The official website is the best way to initially judge the supplier's physique. Although not all silicone factories will publish their own core technologies on the website, but from the company's fortune history Or the motivation and product content introduction and the value areas that the company focuses on can still be understood. Such silicone factories usually have rich and professional knowledge in the selection of silicone raw materials and processing steps, and even insist on them, and can propose the best process suggestions, which indirectly saves the cost and time of customer development.
Advanced and comprehensive equipment
If a worker wants to do a good job, he must first sharpen his tool. Where the silicone factory is willing to invest manpower and capital shows what the company cares about most. It can be imagined that old equipment or process technology that is not up to date will result in poor product quality, low production efficiency, and prolonged delivery time. Silicone rubber suppliers that do not care about these details often do not pay attention to technological innovation or may avoid challenges and thus indirectly reflect a relatively negative attitude towards cooperation. The more common active silicone factories are often keen to participate in equipment exhibitions or technical forums held by relevant industries to exchange the latest intelligence and market information, of course, including new production processes.
Rich practical experience
Having rich practical experience must be an important part of the silicone factory. After all, a product needs to be executed in an experienced silicone factory from mold design to production. Experienced engineers or teachers can avoid low-level mistakes to the greatest extent. Or solve the checkpoint problem in real-time, which greatly shortens the time required for the trial and error process, and also allows customers to avoid many wrong paths. Talent is definitely the most important asset of a company. Generally speaking, a company with a sound system, a good culture, and a proactive company also has the lowest turnover rate, so that employees can continuously accumulate relevant practical experience.
Conclusion
Based on the above, GSUN claims to be a model silicone factory with all four items. In addition to having more than 30 years of experience in contracting silicone products, it has also continuously introduced the latest equipment technology to expand its production capacity. , Process innovation exhibition, without demarcation and self-limitation, while pursuing stability for customers, we will always set more goals and challenges for ourselves. We are Glory Sun, your reliable silicone rubber factory partner. If you have any silicone needs or questions, please feel free to contact us.