BLOG
- Home
- Blog
- Liquid Silicone Rubber
- How liquid silicone rubber work on your demands?
How liquid silicone rubber work on your demands?
October 25,2021
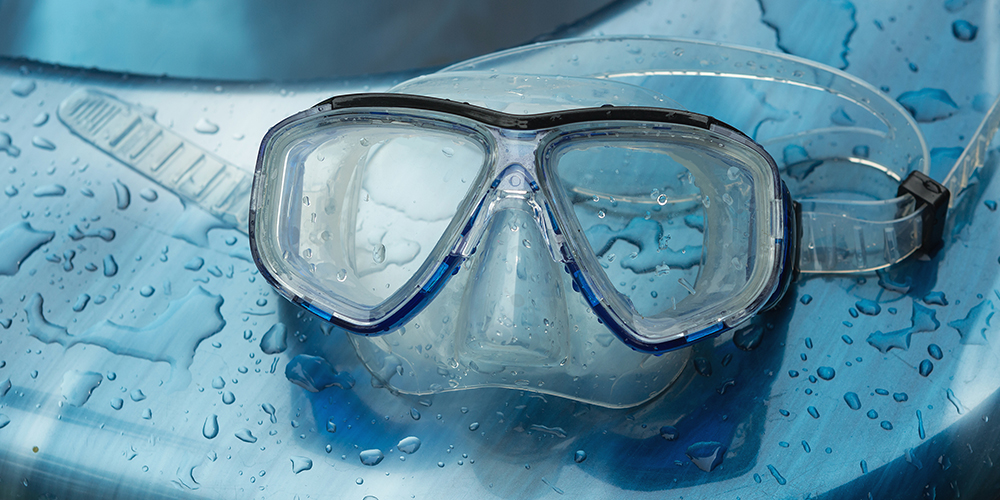
Liquid silicone is also called liquid silicone rubber (LSR). Liquid silicone rubber is named by its liquid form literally and has fluidity. Many people may still feel unfamiliar with liquid silicone rubber. Some even thought that liquid silicone rubber is a new innovative composite material to the market in recent years. However, that may ring your bell if I mention a super common product: Silicone breast implants. The earliest time of the development of liquid silicone rubber can be traced back to 1944. At that time, Dow Corning (now known as DOWSIL), developed liquid silicone cosmetic needles for medical and aesthetic purposes. At that time, the liquid silicone rubber was widely used in the medical beauty industry such as facial, chest injections, and artificial skin applications due to its sterile and high-quality features. Since then, the liquid silicone rubber was introduced into industrial production applications from the late 1970s. Until now, we have seen the rapid growth of the development of liquid silicone in various fields.
What is liquid silicone rubber(LSR)?
Liquid silicone rubber(LSR) is special in its transparent liquid texture. In addition to the most basic safety, non-toxic, waterproof, and other feature, because of its unique fluid form, it can also solve many process limitations that traditional HCR silicone can’t reach--The precision of dimension. In addition, the high transparency texture can produce silicone commodities of clear appearance. Product appearance is very important for certain industries such as medical and optical fields. Finally, liquid silicone rubber needs to be molded under the injection process, this process has almost no burrs, so there is very little waste generated and it is more environmentally friendly. Since liquid silicone rubber and high-consistency silicone rubber are both silicone rubber, what is the difference between them?
(Extension Reading: Liquid Injection Molding (LIM) VS Compression Molding; what fits you best?)
How is liquid silicone formed?
Due to its fluid form, liquid silicone rubber needs to be produced in the same way as plastic injection, actually, the principle is the same as that of plastic injection. The molding steps are: the raw materials(normally packed in barrels) are set up at the feeding place of the injection machine >> the raw materials are feeding to the static mixer for AB material mixing >> injection to the tooling cavity >> tooling heating >> parts completed.
Several features of liquid silicone rubber
High transparency of appearance
Due to the simple processing of liquid silicone raw materials, no additional curing agents and other adjuvants are added, the texture is transparent and pure under a sealed package, which can isolate dust and dirt from the external environment. It can be said to be the purest raw material.
Automatic process
The liquid injection process is automated, which can effectively reduce quality problems caused by human factors. In addition, reducing manpower and labor work can greatly improve production efficiency and relative costs.
High production accuracy
Liquid silicone rubber has better fluidity due to its liquid form. It can completely flow into every corner of the closed tooling cavity. In addition, the silicone rubber injection is fed when the tooling is closed, so there will be no excess burrs generated. The feeding amount of raw materials is also precisely measured by the computer so that you can have better control of the dimensional tolerances.
Environmental friendly
Liquid silicone rubber itself is a non-toxic and safe material. In addition, the production process is almost no by-products such as burrs, which conform to environmental protection requirements and do not cause environmental pollution.
What makes liquid silicone rubber(LSR) and high-consistency silicone rubber (HCR) different?
Material processing
LSR: Mostly known as two-component (AB) liquid silicone rubber. Platinum is used as a catalyst in its raw material vulcanization. The general ratio of AB agents is 1:1 or 10:1, depending on the formula of the raw material manufacturer. The packaging type is commonly seen by barrels, with volume options from 10KG/20KG/25KG to 200KG. After delivery, the raw materials can be directly used for parts production without adding vulcanizing agents or any processing.
HCR: It is a single component silicone rubber, mostly vulcanized by organic peroxides. The raw materials are solidified gel blocks and packed in cartons. After delivery, the raw materials need to go through several processes by the manufacturer according to product specification like mixing the silicone rubber by a mixer with a curing agent added before being put on the production line for molding.
HCR: It is a single component silicone rubber, mostly vulcanized by organic peroxides. The raw materials are solidified gel blocks and packed in cartons. After delivery, the raw materials need to go through several processes by the manufacturer according to product specification like mixing the silicone rubber by a mixer with a curing agent added before being put on the production line for molding.
Manufacturing Procedure
LSR: Just like the injection machine for plastic parts, the liquid silicone rubber is automatically fed through the static mixer of the liquid injection machine (LIM) for AB components mixing, and then injected into the closed cavities of tooling to create the parts.
HCR: Cutting the semi-processed raw material into the appropriate size based on final part figures and put it into the opened tooling, and then close the tooling, then compress it through a hydraulic molding machine under the specific pressure and temperature.
HCR: Cutting the semi-processed raw material into the appropriate size based on final part figures and put it into the opened tooling, and then close the tooling, then compress it through a hydraulic molding machine under the specific pressure and temperature.
Production techniques
LSR: Precisely control the raw material feeding dose into the pre-closed tooling. The tolerance of the final product is small. The burr(flash) is hard to see, the appearance is exquisite, and the automation process is easy to implement. The lowest molding temperature can be under 130°C.
HCR: It takes most of the material preparations manually like cutting the materials and putting them on the pre-opened tooling. The tooling is then closed for molding. That leads to the tolerance being difficult to control, the burr(flash) is bigger, and the parting line needs to be trimmed. A high temperature of more than 180°C is required for parts forming.
HCR: It takes most of the material preparations manually like cutting the materials and putting them on the pre-opened tooling. The tooling is then closed for molding. That leads to the tolerance being difficult to control, the burr(flash) is bigger, and the parting line needs to be trimmed. A high temperature of more than 180°C is required for parts forming.
Appearance
LSR: The transparency of texture is high, the finished product has no obvious parting line, the burrs are not easy to detect by the naked eye. The product has an injection sprue.
HCR: The texture normally appears to be a translucent color with less transparency. The finished product has an obvious parting line. The product does not have any injection sprue.
HCR: The texture normally appears to be a translucent color with less transparency. The finished product has an obvious parting line. The product does not have any injection sprue.
Safety
LSR: Since the liquid silicone rubber is processed in the cleanroom and packed in a sealed container, during the production stage is also fed and injected within an isolated space. The materials were fed into the tool cavity through a closed pipeline, the whole process is not in contact with the outside environment at all, which can fully control the cleanliness of the material to reach the highest degree of purity and eliminate environmental pollution. All of this makes an endorsement of a sense of safety.
HCR: Being a part of silicone rubber member, HCR is also safe and non-toxic. The reason why it is slightly inferior to liquid silicone rubber is mainly reflected in the cleanliness image caused by the difference in the way the material is processed and formed. HCR has lower transparency of texture. It causes problems sometimes when people feel it hard to check the dust or particle through such a milky color surface that leads to unnecessary worry. In addition, the processing of materials of solid silicone rubber requires the addition of vulcanizing agents and other additives, which often results in odors and other phenomena.
HCR: Being a part of silicone rubber member, HCR is also safe and non-toxic. The reason why it is slightly inferior to liquid silicone rubber is mainly reflected in the cleanliness image caused by the difference in the way the material is processed and formed. HCR has lower transparency of texture. It causes problems sometimes when people feel it hard to check the dust or particle through such a milky color surface that leads to unnecessary worry. In addition, the processing of materials of solid silicone rubber requires the addition of vulcanizing agents and other additives, which often results in odors and other phenomena.
Positioning of both LSR & HCR
If there are so many advantages of liquid silicone rubber, why is HCR still taking the highest shares in most industrials and technological industries? It's mainly because each process(injection & compression) has its suitable product applications and market positioning. After realizing the difference between liquid silicone rubber and HCR from the raw material processing to the molding procedure, you should understand that these two can’t be compared under one single rule but put all the factors into consideration such as the product structure, function, market positioning, and development budget. In this way, you are more likely to make the correct decision for your project/products. For example, LSR injection molding requires a relatively low temperature to operate which is 130°C. In this case, it is particularly suitable for plastic + rubber over-molding that is not resistant to high temperatures. From this point of view, liquid silicone rubber is better than HCR. On the contrary, if the product itself is not an exterior part, and the dimensional tolerance accuracy is not required, then it is not necessary to choose the liquid silicone rubber by injection which is relatively expensive. In short, if the compression molding techniques can meet your criteria, there is no need to choose LSR injection molding technology. This also explains why there are so many advantages of liquid silicone rubber, but so far the manufacturing and production of industrial and technological electronics industries are still dominated by HCR.
LSR applications/Scenarios
- Food-grade silicone materials need to be in contact with food and the human body or skin-friendly needs such as maternity and nursing products and kitchenware.
- High transparency and visibility commodities, such as diving equipment, goggles, and oxygen masks.
- Medical grade materials with biocompatible features for medical application, such as medical equipment, diagnostic device, and silicone implants.
- Great precision instruments and products with cleanroom production requirements such as optical products.
HCR applications/Scenarios
- Wide-tolerance-allow industrial parts and automotive accessories. non-complex structured interior components, such as O ring, silicone dustproof cover, silicone water-proof cap, etc.
- Multi-color with many post-processed products, such as TV remote control, calculator instrument or navigation panel, keypads, and buttons.
- Cheap product with simple structure or techniques under a limited budget.
- Small quantities of customized products.
Comparison Chart of liquid silicone rubber(LSR) and HCR
Liquid Silicone Rubber | HCR | |
---|---|---|
Material processing | No additional processing is needed before putting it on the production line. Material packed in a sealed container. | Preparation is needed before putting it on the production line. Material is in a bulk package. |
Product Tolerance | Precise dimension, almost no burr(flash). | tolerance bigger, 0.25mm of burr(flash) is happening. |
Product Appearance | High transparency, no obvious parting line. | Translucent milky white with the obvious parting line. |
Manufacturing Procedure | Material feeding into closed tooling cavity automatically. | Material putting onto opened tooling cavity manually. |
Production techniques | Technically high. | Technically low. |
Environmental protection | High(No waste produced during the production process). | Low(More wasted byproducts during the production process). |
Application | High accuracy and huge volume of products. | non-appearance parts with a bigger tolerance range and limited development budget. |
Conclusion
Through the above introduction, we have learned that there’s no single molding process is absolutely better than another. The point is, what are your needs? If you can luckily select the optimal production process and appropriate raw materials for your product, then half of the problem will be solved. Glory Sun(GSUN) has been devoted to customized liquid silicone rubber and HCR products in the automotive and medical market for decades. We own the tooling house with a tooling design team. The quality of our customers' projects can be fully controlled and guaranteed from the early development stage to the final production. We are committed to providing our clients with the optimal solution to the material selection and tooling design, enabling them to continue business growth. If you do believe and agree that the quality of the tooling will determine the quality of the product, then please contact us! We are Glory Sun!
Article Classification
Recent Articles
- Applications of Liquid Silicone Rubber Injection Molding in smart clothing
- Discover the Versatility and Benefits of Liquid Silicone Rubber (LSR)
- The Application of Liquid Silicone Rubber in Seals and Gaskets
- Applications of Liquid Silicone Rubber in Medical Devices
- The Future of Liquid Silicone in Automotive Applications