- Home
- Blog
- Production & Lab
- What is Two Shot Molding?
What is Two Shot Molding?
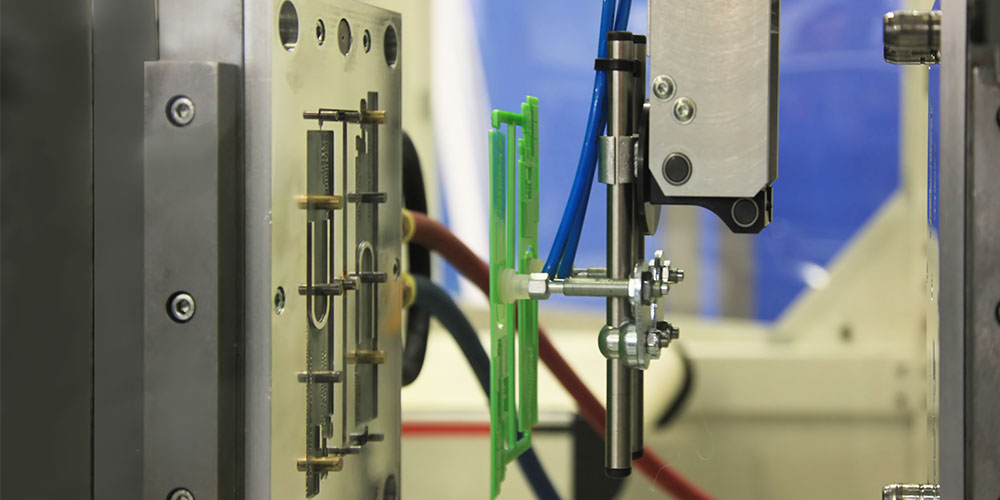
If there is no rubber and plastic in our life, our shoes will become inflexible, communication equipment will not be able to use, and even the car will not be able to operate normally. Among them, coating injection plays a key role in the electronics, medical, automotive and aviation industries to meet our needs for food, clothing, housing, transportation, and entertainment. What is two shot molding? Is it different from general injection molding? Our easy-to-understand explanations and arrangements allow you to understand.
What is the principle of two shot molding?
Like general injection molding, two shot molding requires the material to be melted at a high temperature in the filling tank, and then injected into the mold through the internal screw for shaping. The feature of two shot molding is that it can produce two different materials at one time. The common technology is to inject a relatively hard rubber or plastic housing first, and then move it to another mold immediately, and inject a soft elastomer to coat it, which is called two shot molding. The steps sound simple, but it is not easy to complete. It needs to be equipped with a dedicated machine and more complex molds to achieve. Although the initial investment cost of two shot injection molding is higher than that of injection molding, the benefits and features of two shot molding can bring greater profits to the market.
The benefit of two shot molding?
Good user experience and aesthetic looking
Two shot molding can combine two different materials to make the product easier to use. For example, in the handle part of a toothbrush or hand tool, coating a hard frame with a soft material can provide users with better tactile and anti-slip effect. Even if the colors of the raw materials are different, the process of two shot injection molding will not stain each other, and the design of the product appearance is more flexible.
Reduce processes and improve efficiency
Generally, the injection machine usually only has one filling slot, while the two shot injection machine has more than two. When the injection product has two or more materials combined, it is generally necessary to move the semi-finished product after the frame is injected from one machine. to the second machine for co-injection; but the professional two shot injection machine can condense these processes in one machine. Since it is on the same machine, the process is automated. The biggest advantage is that it can avoid manual loading and unloading and assembly mistakes, and greatly improve production efficiency. It seems that the investment threshold is high, but in terms of long-term investment in machines, it is It saves money for the company.
Products are more durable
For delicate electronic products, Two shot molding can isolate important parts of the product from air and water according to the material, and even prevent the influence of electricity and heat, allowing electronic products to operate in the most stable environment. Compared with traditional manual assembly parts, the two shot molding products have better performance in fineness and tightness. In addition, the elastic body itself has the function of absorbing vibration and fixing parts, which can prevent large shaking such as electric drills. The power tool disintegrated due to vibration.
Combination of Material for Two Shot Molding
As mentioned earlier, the two shot molding is mostly a combination of hard materials and soft materials. Which materials belong to hard materials? Which materials are soft materials? Among them, there are dozens of raw materials that can be used for two shot injection molding. Here are the six common ones:
Commonly used hard material:
PE
The composition of PE plastic is polyethylene, which is the most common plastic in our daily life. Almost all plastic bags and opaque plastic containers that are commonly seen are the products of PE plastic. The reason why PE plastic is so widely used is because its properties are very stable, heat-resistant, corrosion-resistant, high in hardness but low in friction, which can meet most applications and become one of the common materials for two shot injection molding.
ABS
The characteristics of ABS plastic are mainly determined by three chemical substances, acrylonitrile, butadiene and styrene. By increasing the proportion of specific substances, the corresponding performance can be improved. For example: ABS plastic with a high proportion of acrylonitrile is quite heat-resistant and can be used in products such as hair dryers or irons; a little more butadiene can be used in safety helmets that need impact resistance; and styrene has a higher proportion , you can create thinner ABS products, such as mobile phone protective cases. The high adjustability of ABS plastic is used in a wide range of fields, from heavy industries such as automobiles and aerospace to daily necessities.
PA
The composition of PA plastic is polyamide, but perhaps the more familiar name is "nylon". PA plastic has high hardness, heat resistance and electrical insulation, so it is often used to produce industrial products and daily household appliances, such as electric drills, industrial fans, household vacuum cleaners, electric cookers, PA plastics play the role for all of them.
Commonly used soft material:
TPU
TPU is also known as thermoplastic polyurethane. It has excellent wear resistance, weather resistance, oil resistance and elasticity. It is not only often used in high-wear products such as shoe soles and wheels, but also a very good coating injection material. , The characteristic is that it can protect the gap between the parts from external substances and thus prolong the life of the product. It can be co-molded on the related equipment to increase the friction, so that the user can hold it well without slipping.
TPR
The full name of TPR is called thermoplastic rubber elastomer. This is a material that has a texture close to rubber and silicone. It is one of the best in softness among many thermoplastic elastomers. In addition, this material is easy to color and not easy to fade. It is not toxic. , suitable for making high elastic insoles, skin-friendly medical gloves and children's toys. TPR material can also be combined with other additives to improve the hardness or tensile strength, etc., and this material is highly environmentally friendly and can be recycled and reused, so it is also one of the high-profile co molding injection materials.
Silicone Rubber
Silicone rubber is soft and non-toxic and can withstand temperatures from 220°C to -40°C, making it ideal for making containers, conveyor rails and related contact products for the food processing industry. The waterproof and electrical insulation properties of silicone make it popular in electronic products. Not only can it block the contact between the inside of the product and the outside world, but the elasticity of silicone can also improve the service life of electronic products.
〈Extension Reading: How is silicone rubber molded?〉
Application of two shot molding products
Automotive industry
There are many equipment in the interior parts that need to combine multiple materials, such as: control panels such as windows, sounds, and screens. This type of equipment often needs to overcome the situation of high temperature and high ultraviolet rays, so it is very suitable to use soft and hard materials that are resistant to sunlight and high temperature, such as ABS plastic combined with silicone rubber. For the automotive industry, two shot molding can improve the precision of workmanship and further reduce costs, which has many benefits.
Medical industry
The products of the medical industry can be roughly classified into two categories. The first is consumable products, including plastic tubes, syringes, aseptic packaging, etc., which need to meet the conditions of low cost and non-toxicity as much as possible. Taking the piston of the injection syringe as an example, the part of the push rod is made of low-cost and stable PE plastic, combined with a soft rubber pad, which can save manual assembly time and reduce the cost of disposable consumables by covering the injection. The second is artificial blood vessels, artificial joints, etc. In addition to non-toxic and precise dimensions for these implantable medical organs, most of these devices must be combined with a variety of materials to function, so two shot injection molding is arguably the best solution.
Electronic industry
There are many small parts in electronic equipment. The traditional production method is to produce a large number of parts through molding, and then manually assemble them in the way of home OEM. The product can be completed without special technology. However, as the parts of electronic products become more and more precise, and the number of components is also increasing, the advantages of coating and injection are becoming more and more critical, including: reducing processes, improving dimensional accuracy, and higher adhesion than manual bonding, etc. It is a trend that two shot molding injection is becoming more and more popular in the electronics industry.
Conclusion
Two shot molding is one of the injection methods. Although the initial investment is relatively high and requires more mold professionals than ordinary injection to design high-quality products, it is the most affordable choice for composite materials in terms of long-term investment. Regardless of the injection method, a rigorous process is required. Raw material control, mold design, injection monitoring and quality inspection are closely linked to each other. If there is no consistent standard, time and money will be lost. GSUN Electronics provides one-stop service, from receiving inquiries to product delivery, and our raw materials are all from the highly reputable Japan Shin etsu, German Wacker and American Dowsil, and our products have passed ISO14001, ISO9001, ISO13485, IATF16949 and other professional quality certifications, At the same time, he also masters a variety of technologies such as 2-shot injection, general injection, and compression molding. With rich practical experience, we can tailor the most suitable, economical and efficient production process for customers.