- Home
- Blog
- Silicone Rubber Introduction
- How is silicone rubber molded?
How is silicone rubber molded?
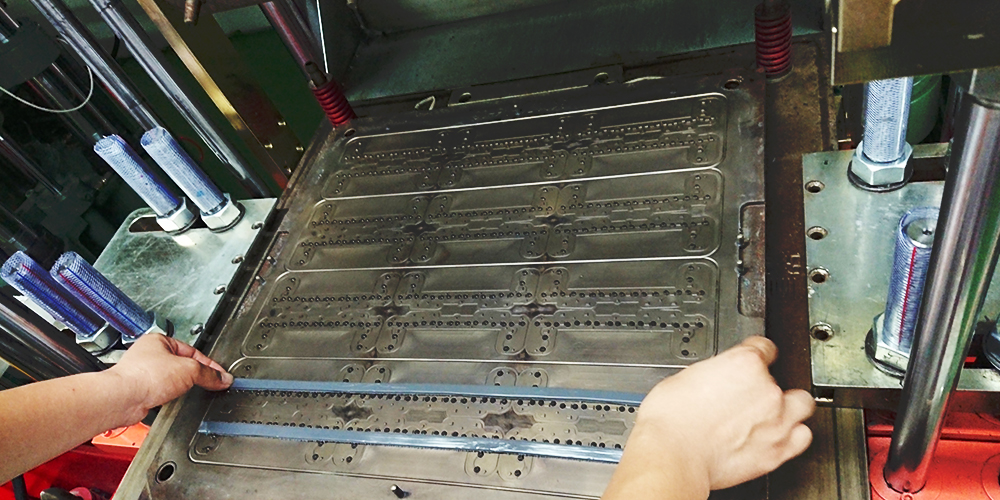
Silicone products have become inseparable from our daily lives, the applications range from foods contact products, such as silicone rubber spoons, silicone lunch boxes, silicone water cups, to the accessories such as silicone watch Fitbit, silicone earphone plugs, and even medical equipment and auxiliary materials related to safety. And so on, with all of those can not ignore the contribution of silicone rubber. However, you must be curious about what types of silicone rubber are divided into and what process methods are suitable more for each specific type of silicone rubber. Why is it important to know? Because it determines whether a project is in the correct direction at the earlier development stage. It is also a primary factor in the success of the project. Understanding the silicone molding method will save you a lot of wrongdoing.
What is silicone rubber molding?
What are the types of silicone rubber?
High-consistency silicone rubber (HCR)
Its raw material is solidified texture, like block gum, and the appearance is generally milky white. The conventional hardness is about 30-70 shore A, and some special products will require 80-90 shore A. These will be modulated during the raw material processing and mixing stage, and the products with special color requirements will also be mixed with color pigment at this stage. Most of the daily necessities and consumer electronics products on the market are made of this type of silicone molding. On the other hand, the material cost is more competitive.
(1).jpg)
Liquid silicone rubber(LSR)
The raw material is in the form of a liquid water paste, with a transparent appearance and texture, almost as clear as water. Commonly used hardness is 10-20 shore A, some special products will require 50-60 degrees, but it is not common, and not recommended, because the increase in hardness will slow down the fluidity of the raw materials and cause poor quality. Generally, silicone molding products using liquid silicone rubber as the raw material have no post-process and coloring requirements, so that the unique feature of the high transparency of the raw material won't be hidden. So it is easy to understand that the liquid silicone rubber somehow compensates for the specific limitations (transparency and softness) of the solid silicone rubber itself. Since liquid silicone rubber is more expensive than solid silicone rubber, it doesn't be used so commonly. At present, it is still used in products with higher precision and high-value products, such as the optical and medical categories, so its popularity is not as high as that of solid silicone.
.jpg)
Two common silicone rubber molding methods
Compression Molding
Liquid Injection Molding
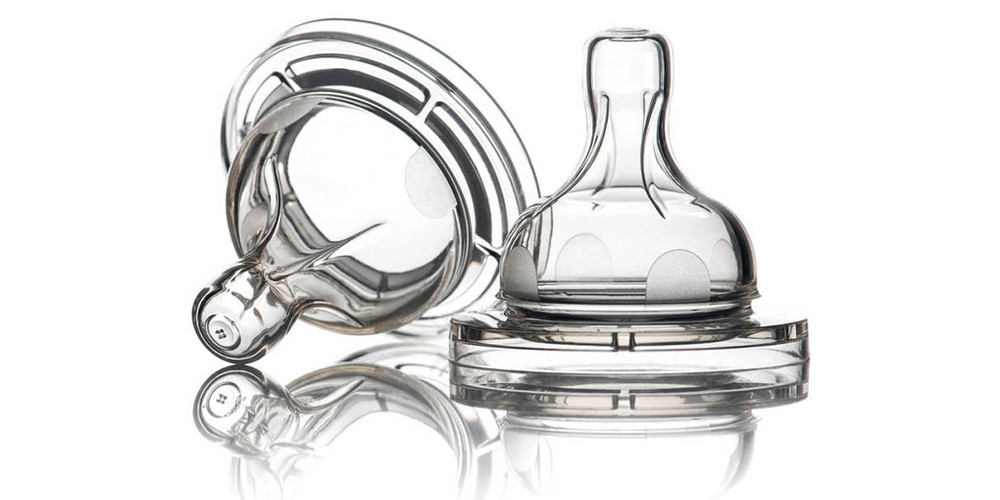
Comparison chart of two molding types
Compression Molding | Liquid Injection Molding | |
---|---|---|
Product feature | Has obvious parting line, without injection sprue. | No obvious parting line, with injection sprue. |
Production techniques | Technically low with more manual operation. | Technically high, can be produced automatically. |
Applications | Silicone rubber buttons/keypads for remote controls and other electronic devices, interior parts that do not require precise appearances, such as O-ring waterproof rings, silicone molding products with low precision or high tolerance, silicone parts with multi-color processes. The larger size of silicone parts such as jelly protective cover, dust cover. | Products that require high transparency, such as optical products, diving goggles, and oxygen masks. High-precision parts with fine appearance dimensions, such as automotive lamp silicone rings, medical equipment, and biocompatible implant products. |
Cost | The development cost of raw materials and tooling is low, but due to the large labor demand and high defective rate, the unit price of the product won't be cheaper in the long run. | The development cost of raw materials and tooling is relatively high, but the automatic production increases the production efficiency and yield rate which causes the unit price of products cheaper in the end. |