PRODUCT SERVICE
- Home
- Product Service
- Liquid Silicone Rubber (LSR)
- LSR Single Shot
Liquid Silicone Rubber (LSR)
LSR Single Shot
- Features
- Biocompatibility: Liquid silicone rubber has good compatibility with the human body and body fluids. Compared with other types of materials, liquid silicone rubber has the good antibacterial ability and will not stain. Liquid silicone rubber is also odorless and can be formulated as raw materials for silicone injection molding(LIM) in accordance with strict FDA requirements. The material can be sterilized by a variety of methods, including steam autoclaving, ethylene oxide (ETO), laser light, and many other technologies.
- Durability: Liquid silicone rubber(LSR) parts can withstand extreme temperatures, which makes them ideal for car engines and surrounding components. Parts manufactured by liquid silicone injection molding can withstand high temperatures and are not easy to melt.
- Chemical resistance: Liquid silicone rubber is water, oxidation resistance, and some chemical solutions, such as acids and alkalis.
- Temperature resistance: Compared with other elastomers, LSR injection molding can withstand a wide range of extreme high/low-temperature conditions.
- Mechanical properties: Liquid silicone rubber has good ductility, high tearing and tensile strength, and excellent flexibility.
- Electrical properties: Liquid silicone rubber has excellent insulation properties, providing a new choice for many electrical and power-related applications. And compared with traditional insulating materials, silicone rubber can work at higher and lower temperatures.
- Transparency and pigmentation: Liquid silicone rubber has natural transparency, which makes it qualified for a high standard of appearance products and multi-color mixture.
Description
Liquid Silicone Rubber has existed since the late 1970s and has become the supreme choice for the manufacture when choosing the material of rubber commodities. The unique quality of liquid silicone injection molding makes it different from traditional high-consistency silicone and other plastic molding processes.
Application
Liquid silicone rubber has many excellent physical properties with a wide range of applications, including medical treatment, automobiles, daily necessities, etc, And many precision industrial applications, such as machine valves, instrument panels, diaphragms, etc. The silicone rubber injection molding is the best option for high-end medical equipment. For example, the inflatable balloon of the Endorectal coil MRI is very rigorous in appearance smoothness and burrs, making liquid silicone rubber the first choice for relative solutions.
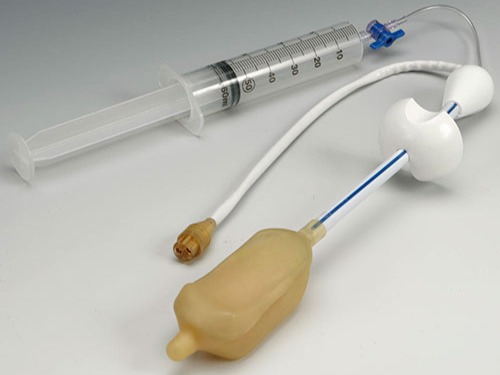
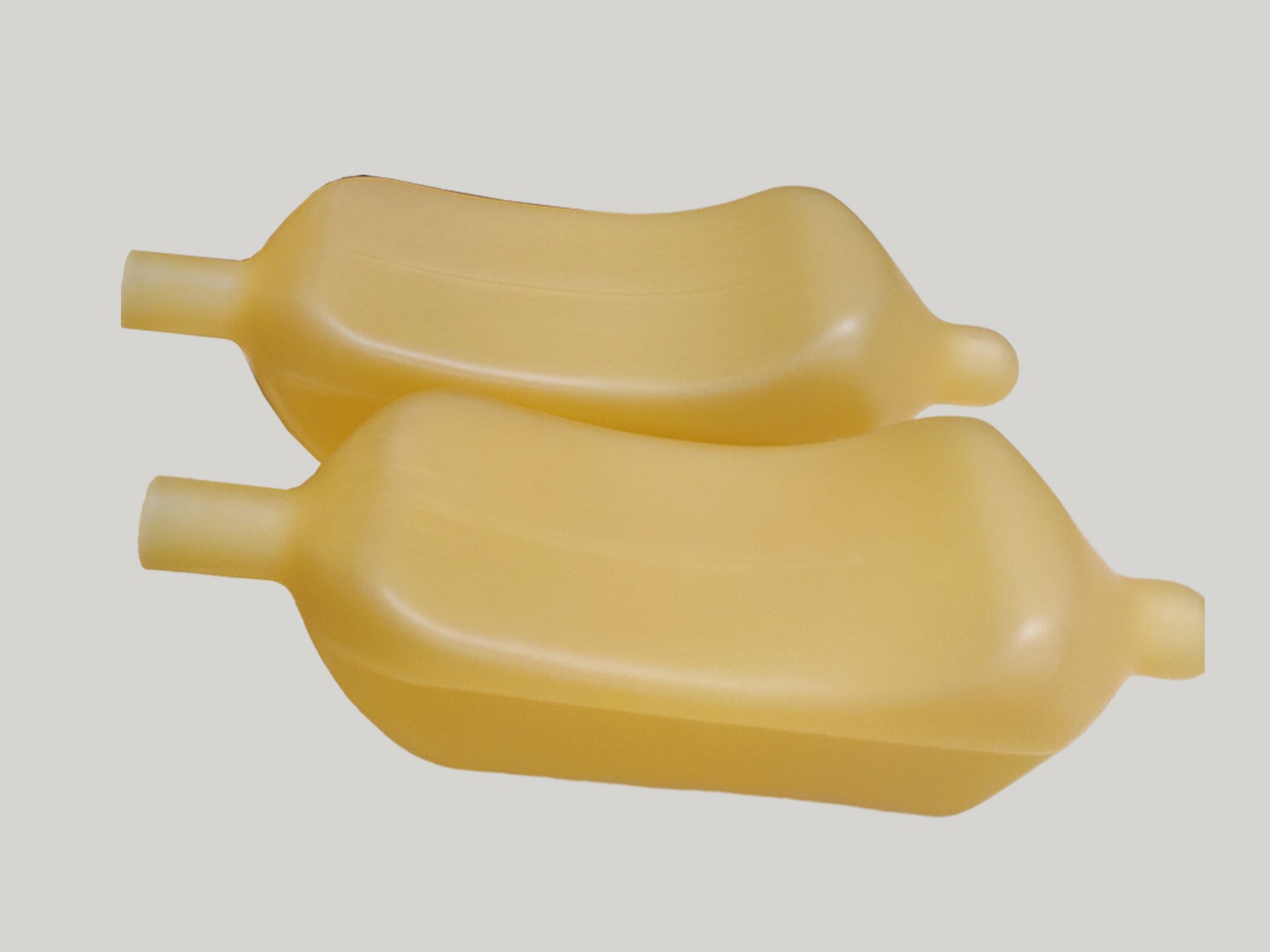
What is LIM process?
Liquid injection molding (LIM) is an industrial fabrication process that molds materials into a broad range of components and products. Unlike the standard reaction injection molding process, which relies on pressurized impingement mixing, liquid injection molding uses a mechanical mixing process that focuses mainly on liquid silicone rubber (LSR) and similar elastomeric materials.Why LSR?
Liquid silicone rubber (LSR) is frequently used in injection molding by demanding manufacturers. While not the right choice for every application, it offers a number of advantages that make it an option worth considering in many situations. Here are advantages you need to know about LSR:Compare List | LIM(LSR) | HCR(HTV) |
---|---|---|
Material mechanical property | Supreme compression set and elongation, higher tear and tensile strength. | Good compression set and elongation, high tear and tensile strength. |
Hardness | 10 shore A - 90 shore A | 25 shore A - 90 shore A |
Working temperature | - 40oC to 230oC | - 40oC to 230oC |
Material | good insulation | good insulation |
Bio-compatibility | good food, water and medical contact, safe applications | Using for daily accessories , but can’t be implanted into body skin and blood |
Transparency | High Transparent | Low Transparent |
Forming way | Injection Mold | Compression Mold |
Technological Process | Simple (Automatically) | Complex (Labor) |
Forming Time | 20-120 Seconds | 60-800 Seconds |
Production Efficiency | High | Low |
Precision | High, no flash | Low , few flash |
Stability | High | Low |
Waste | Little | Much |
Workshop | Clean, dust-free | Clean room |
Advantageous to Environmental Protection
No by-product is generated in the curing process. Additionally, due to burr-free, runner-less forming, no waste material is generated in the production process and it is advantageous to environmental protection.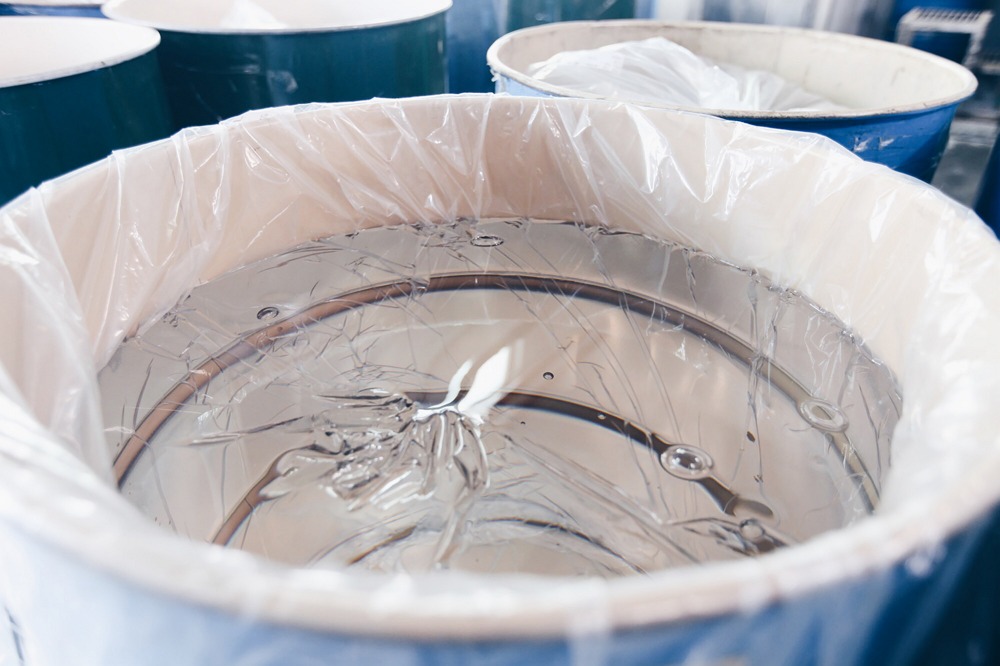