- Home
- Blog
- Liquid Silicone Rubber
- All Types and Applications of Silicone Injection Molding
All Types and Applications of Silicone Injection Molding
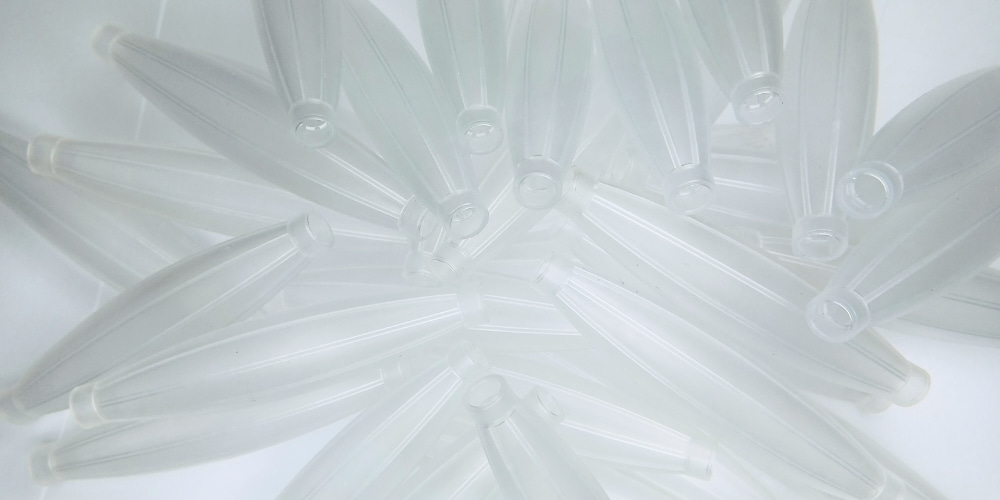
Silicone injection molding is a method used to manufacture high-quality silicone products. It encompasses various techniques such as single-shot injection, insert molding, and two-shot injection. These techniques are widely applied in various industries such as healthcare, automotive, aerospace, electronics, and toys, etc.
〈Extended reading:What You Should Know About Silicone Rubber 〉
〈Extended reading:Liquid Injection Molding (LIM) VS Compression Molding; what fits you best? 〉
What is Silicone Injection Molding?
Silicone injection molding is a highly efficient method for manufacturing silicone products which includes three types: single shot injection, insert molding, and two-shot injection. The process involves injecting raw liquid silicone material into the mold and shaping it under high pressure. This technique is commonly used for producing high-quality and high-precision products, as it allows for the creation of complex geometric shapes while maintaining control over the product's dimensions and thickness. The type of silicone injection can be selected according to the application to creat suitable products.
〈Extended reading:How is silicone rubber molded? 〉
Types of Silicone Injection Molding
Silicone injection molding encompasses several different types, including single-shot injection, insert molding, and two-shot injection. Here is a detailed description of these types, including their features, advantages and disadvantages:
Single-Shot Injection
Single-shot injection refers to the use of a single type of silicone material for the injection molding process. It is the most commonly used silicone injection molding method. The key characteristic of this technique is its fast molding speed, allowing for the production of high-precision and high-quality products. Additionally, single-material injection machines are relatively easy to maintain and operate. However, one limitation of this method is that it cannot produce multi-colored or multi-hardness products since only one material is utilized.
Liquid silicone single-shot injection process is a specialized injection molding technique used for manufacturing silicone products. It involves the use of a single liquid silicone material without the need for mixing different components. The general steps of the liquid single-material injection molding process are as follows:
Material Preparation
Select the appropriate liquid silicone material, and formulate and adjust it according to the product requirements. Ensure the accurate preparation and proportioning of the material.
〈Extended reading:Applications of Liquid Silicone Rubber Injection Molding in smart clothing 〉
Preheating
Control the temperature of the injection molding machine's barrel to be below 25 degrees Celsius to ensure smooth flow and proper filling of the silicone material into the mold.
Mold Preparation
Prepare the appropriate mold, including steps such as cleaning the mold and applying mold release agent, to ensure smooth demolding of the product.
Silicone Injection Molding
Inject the liquid silicone material (AB glue) into a static mixer and then transfer it to the injection device. During the injection process, the material is injected into the heated mold.
〈Extended reading:Anti-Static Silicone: Key Factor in Static Control 〉
Mold Filling
By applying the appropriate injection pressure and speed, the liquid silicone fills the entire mold cavity. The mold temperature should be evenly heated to ensure a stable flow of the silicone material within the mold and prevent issues such as incomplete filling.
Curing
Once the silicone has been filled into the mold, the silicone material inside the heated mold begins to cure and harden.
Demolding and Post-Processing
After a sufficient curing time, the mold is opened, and the finished product is removed. Post-processing of the product may include trimming edges, removing burr, and cleaning, etc.
Liquid silicone single-material injection molding process offers several advantages, including simple operation, high production efficiency, and consistent product quality. It is widely utilized in the manufacturing of silicone products, including seals, buttons, handles, electronic component encapsulation, and various other application areas.
〈Extended reading:The Application of Liquid Silicone Rubber in Seals and Gaskets 〉
Insert Injection Molding
Insert silicone injection molding refers to the process of injecting other materials, such as metal or plastic, into the interior of a silicone product to enhance its functionality or connectivity. The key characteristic of this technique is the ability to create silicone products with embedded or connected components. However, since additional materials need to be injected, insert molding generally takes longer molding time and incurs higher costs compared to single-material injection.
Liquid silicone insert molding process is a specialized silicone molding technique commonly used to embed other materials or components within silicone products. Here are the general steps involved in the liquid silicone insert molding process:
Material Preparation
Prepare the liquid silicone and the materials or components to be inserted. Adjust the formulation and properties of the silicone according to the product requirements.
Mold Preparation
Prepare the appropriate mold, including the silicone part and the space for the materials to be inserted. Ensure the mold surface is clean and apply mold release agent for easy demolding.
Silicone Injection
Inject the liquid silicone into the mold, filling it to a certain extent to ensure complete coverage of the materials to be inserted.
〈Extended reading:Discover the Versatility and Benefits of Liquid Silicone Rubber (LSR) 〉
Placement of Materials or Components
Gently place the materials or components to be inserted into the silicone. Ensure their position and orientation are correct.
Silicone Filling
Continue injecting the liquid silicone until the mold is completely filled, covering the materials or components to be embedded.
〈Extended reading:Behind the Scenes: Backlit Silicone Keypad Technology 〉
Curing
Once the silicone filling is complete, the silicone inside the heated mold begins to cure and harden. The curing time depends on the characteristics and thickness of the silicone.
Demolding and Post-Processing
After curing, open the mold and remove the finished product. Perform post-processing on the product, such as trimming edges, removing burr, and cleaning, etc.
The insertsilicone injection molding process allows for the embedding of electronic components, plastic parts, metal parts, and other materials within silicone products. This technique is widely used in fields such as electronics, medical devices, automotive, and consumer goods, offering greater design range and functionality.
〈Extended reading:The Future of Liquid Silicone in Automotive Applications 〉
Two-Shot Injection
Two-shot silicone Injection molding refers to the simultaneous use of two different types of silicone materials for injection molding to create products with multiple colors or hardness levels. The key feature of this technique is the ability to manufacture products with various colors or hardness variations. It offers faster molding speeds and is suitable for applications that require different physical properties. However, due to the need for specialized injection machines, the molding precision may be lower, and the machines can be more costly to maintain.
Two-shot injection is a specialized silicone injection molding technique used for manufacturing silicone products, utilizing two different liquid silicone materials for molding. The following are the general steps involved in the liquid two-shot injection process:
〈Extended reading:Cultivating a Deeper Understanding of Silicone Hardness 〉
Material Preparation
Prepare two different types of liquid silicone materials and adjust their formulations according to the product requirements. Ensure accurate preparation and proportioning of the materials.
Preheating
Maintain a specific low temperature in the barrel of the injection molding machine to ensure smooth flow and filling of the two silicone materials.
Mold Preparation
Prepare suitable molds, including cleaning and applying mold release agents, to ensure smooth demolding of the products.
Silicone Injection Molding
Inject the two liquid silicone materials into different barrels of the injection molding machine. During the injection process, they are separately cooled and injected into the mold through the nozzle.
〈Extended reading:Understanding Thermal Silicone Rubber: A Comprehensive Guide 〉
Mold Filling
Utilize appropriate injection pressure and velocity to ensure that the two liquid silicone materials are filled into different areas of the mold, accurately replicating the shape within the mold.
Curing
Once the two silicone materials are filled, the silicone within the heated mold begins to cure and harden.
Mold Removal and Post-processing
After sufficient curing time, the mold is opened, and the finished product is taken out. Post-processing is performed on the product, such as trimming edges, removing burr, cleaning, etc.
The dual-shot silicone injection molding process enables the manufacturing of silicone products with different hardness, elasticity, colors, and characteristic. It is widely used in applications that require products with multiple layers or different performance zones, such as seals, buttons, handles, electronic encapsulation, and more. This process provides greater design flexibility, allowing for more functional and diverse products.
〈Extended reading:Is Two Shot Injection same as Insert Injection? 〉
〈Extended reading:What is dual-shot injection? An article understanding its principles and advantages 〉
Comparison of Silicone Injection Molding
Types |
Characteristic |
Advantages |
Disadvantages |
---|---|---|---|
Single Shot Injection |
Single type of silicone rubber |
Fast injection speed, high molding accuracy, and simple maintenance. |
Unable to produce multi-colored or multi-hardness products. |
Insert Injection |
Injecting other materials into silicone rubber |
Ability to create inserts |
Longer molding time and higher cost. |
Two Shot Injection |
Simultaneous use of two types of silicone rubber |
Ability to produce multi-colored or multi-hardness products, and fast molding speed. |
High equipment cost and complex maintenance. |
The five major application areas of silicone injection molding:
Silicone injection molding is widely used in various industries, including medical, automotive, aerospace, electronics, and toy industries. Here are detailed descriptions of some of these industries:
Application Area 1: Medical Industry
Silicone injection molding is widely used in the medical industry. It can produce high-quality medical devices and instruments such as surgical gloves and respirators. Since silicone itself is an excellent biocompatible material, instruments made of silicone are less likely to cause allergies or other adverse reactions. Silicone also exhibits high wear resistance and corrosion resistance, making it capable of withstanding common cleaning methods such as disinfection and sterilization. Additionally, the flexibility and elasticity of silicone materials contribute to the comfort and safety of gloves and other instruments.
〈Extended reading:Medical Grade Silicone: How to define it? 〉
Application Area 2: Automotive Industry
Silicone injection molding technology has also found widespread applications in the automotive industry. It can produce excellent automotive components such as car lights, dashboards, air deflectors, and hoses. Silicone is known for its high temperature resistance and abrasion resistance, making it highly suitable for automotive parts production. Additionally, silicone materials exhibit good weather resistance and chemical stability, enabling them to withstand UV radiation and various forms of chemical corrosion, thereby extending the lifespan of automotive components.
〈Extended reading:How the silicone industry achieve net-zero carbon emissions goals 〉
Application Area 3: Aerospace Industry
Silicone injection molding technology can be found in the aerospace industry, where it is known for producing highly precise and complex components. For example, aircraft engine and wing components require materials of high quality and reliability, making silicone injection molding an ideal choice. This technique allows for the production of parts that meet intricate design requirements while offering exceptional durability and fatigue resistance. These components can withstand extreme conditions such as high altitudes, low temperatures, and high pressures.
Application Area 4: Electronic Industry
Silicone injection molding technology is widely used in the electronics industry due to its ability to produce products with excellent protection and waterproofing capabilities. For example, products such as phone cases and battery enclosures require protection for internal circuits and batteries while also being waterproof to enhance their lifespan and safety. Silicone injection molding can produce products that meet these requirements and provide flexibility and elasticity, thereby increasing the comfort and durability of the products.
〈Extended reading:Silicone Rubber OEM Manufacturers – Glory Sun Group 〉
Application Area 5: Toy Industry
Finally, you will also find that certain toy products are made using silicone injection molding. The soft and elastic characteristics of silicone make it suitable for many small toys such as Barbie dolls, baby toys, and care products. Silicone injection molding can produce toys that meet these requirements while providing excellent safety performance and durability, ensuring that the toys can be used safely and are long-lasting.
〈Extended reading:Is Silicone Toxic? A Comprehensive Analysis of Silicone Safety 〉
Common Issues in Silicone Injection Molding
What is the advantages of silicone injection molding?
Silicone injection molding technology offers several advantages such as fast production speed, high precision, high production efficiency, stable product quality.Silicone injection molding has several advantages, including:
Design Flexibility
Silicone injection molding can produce products with complex shapes, including slender structures, thin-walled components, and microstructures. This tecnique enables high precision in dimensions and details and can manufacture products that are difficult to achieve with other traditional molding methods.
〈Extended reading:Conductive Silicone Strips: The Ideal Choice for Efficient Conductive Solutions 〉
High Quality and Consistency
During the silicone injection molding process, the material is uniformly filled into the mold cavity and maintains consistent dimensions and performance during the curing process. This ensures high-quality, consistent, and reliable products.
Material Characteristics
Silicone rubber possess excellent characteristics such as exceptional elasticity, high temperature resistance, chemical corrosion resistance, and insulating properties. Silicone injection molding can retain these properties, making the products suitable for a wide range of applications.
〈Extended reading:High-Temperature Silicone: Characteristics, Applications, and Buying Guide〉
High Production Efficiency
Silicone injection molding offers the advantage of fast production. Once the mold design is completed and validated, the production process can be highly automated, enabling continuous and efficient production. This improves production efficiency and reduces costs.
〈Extended reading:How to choose between TPE and Silicone Rubber? Find out their respective characteristics! 〉
Flexibility and Design Freedom
Silicone injection molding enables flexible product design and rapid product iteration. Designers can adjust the shape, size, hardness, color, and other characteristics of the product according to their needs, thus meeting different customer requirements. This allows for greater design freedom and customization options.
In summary, silicone injection molding offers advantages such as the ability to produce complex shapes, high quality, superior material properties, high production efficiency, and strong flexibility. These advantages make it an ideal choice for a wide range of applications in industries such as electronics, medical, automotive, consumer goods, and more.
What are the common silicone materials used in silicone injection molding?
Common silicone materials used in silicone injection molding include silicone rubber, methyl silicone rubber, and butyl silicone rubber.
〈Extended reading:What is the common elastomeric silicone? here is some tips you can't miss out 〉
General silicone rubber
Also known as standard silicone, it is widely used in various products. It possesses excellent elasticity, flexibility, and high-temperature resistance. General silicone is typically available in different hardness to accommodate different application requirements.
〈Extended reading:Is Silicone Rubber Better Than Rubber? 〉
High transparency silicone rubber
This type of silicone rubber exhibits extremely high transparency and optical properties, making it suitable for products that require transparent or translucent effects, such as lighting products, optical components, and more.
Flame-retardant silicone rubber
This type of silicone rubber possesses excellent flame retardant properties and can suppress the spread of flames at high temperatures. It is commonly used in electronic products and automotive components where flame retardancy is required.
Medical-grade silicone rubber
This type of silicone rubber exhibits high biocompatibility and medical safety, complying with relevant standards and requirements for medical devices. Medical-grade silicone is widely used in medical equipment and products such as catheters, artificial organs, pharmaceutical storage containers, and more.
〈Extended reading:What is Conductive Silicone Rubber? Learn it from silicone and conductivity! 〉
High-strength silicone rubber
This type of silicone exhibits higher tensile strength and tear strength, making it suitable for applications that require superior mechanical performance, such as automotive seals, industrial components, and more.
Above silicone rubber options are just a few common types used in silicone injection molding. Depending on specific application requirements, there can be other specialized formulations and customized silicone rubber available.
How to achieve color diversity in silicone injection molding?
Achieving color diversity requires the use of different silicone materials and color additives. By adjusting the ratios and combinations, it is possible to create products in different colors.
Silicone injection molding can achieve color diversity mianly through the following methods:
Adding Pigments
Adding pigments to silicone materials is a common method to achieve color diversity. Pigments can be in the form of solid powders or liquids, and by mixing them with silicone rubber, silicone materials of different colors can be obtained. This method allows for a wide range of color options.
〈Extended reading:What is Solid Silicone HTV 〉
Dyeing agents
In addition to adding pigments, dyeing agents can also be used to change the color of the silicone rubber. Stains interact with the silicone molecules to give them the desired color. This method is often used in some special applications, such as the need to identify specific areas or color distinctions in medical devices.
〈Extended reading:Applications of Liquid Silicone Rubber in Medical Devices 〉
Printing and spraying
For some products that require complex patterns or special effects, printing and spraying techniques can be used to add color to the surface of the silicone. This can be achieved by spraying paint, using printing techniques or applying special color treatments.
Color mixing
During the silicone injection molding process, silicone materials of different colors can be mixed to obtain a color mixing effect. This method can achieve the effect of gradient color, color transition or multi-color mixing.It should be noted that the transparency of the silicone material will also affect the final color rendering effect.
For clear or translucent silicone products, the color may appear lighter or slightly transparent.Overall, silicone injection molding can achieve a variety of colors to meet the color requirements of different applications.
〈Extended reading:What is eco-friendly silicone? An analysis of its 4 key material advantages and applications! 〉
Conclusion
Silicone injection molding is a widely used molding technique that offers various injection types. It is characterized by fast production speed, high production accuracy, flexible design, and excellent material performance, making it extensively applied in many different industries. If you are interested in silicone products, you can consider the manufacturing services provided by Glory Sun Group. We are a leading manufacturer of custom silicone products, offering related professional services. We not only produce high-quality products, but also prioritize a streamlined and efficient service process, which is another prominent feature. If you have any requirements, please feel free to contact us immediately.
〈Extended reading:4 Tips for Choosing A Silicone Rubber Suppliers 〉
Article Classification
Recent Articles
- Applications of Liquid Silicone Rubber Injection Molding in smart clothing
- Discover the Versatility and Benefits of Liquid Silicone Rubber (LSR)
- The Application of Liquid Silicone Rubber in Seals and Gaskets
- Applications of Liquid Silicone Rubber in Medical Devices
- The Future of Liquid Silicone in Automotive Applications