シリコーン射出成形のあらゆる種類と用途
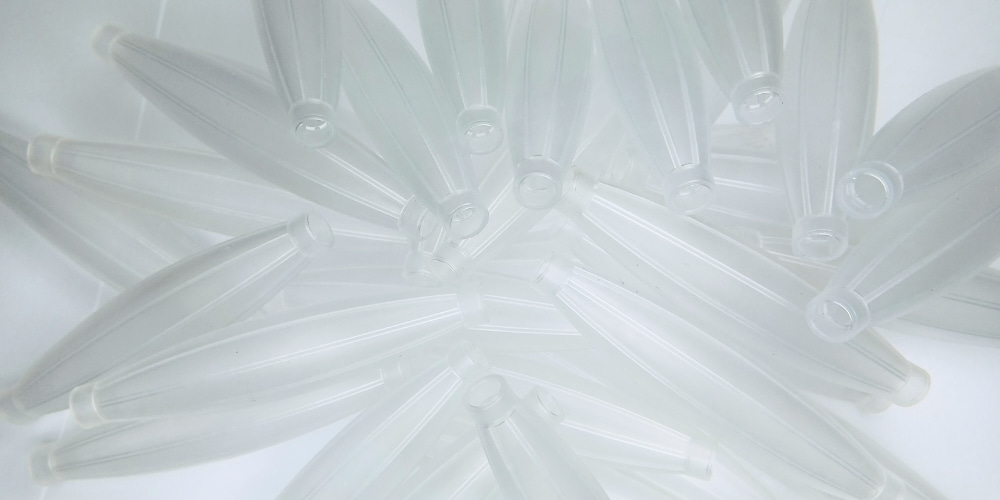
シリコーン射出成形は、高品質のシリコーン製品を製造するために使用される方法です。シングルショット射出成形、インサート成形、ツーショット射出成形など、様々な技術を包含しており、これらの技術は、ヘルスケア、自動車、航空宇宙、電子機器、玩具など、様々な業界で広く応用されています。
〈関連記事: シリコーンゴムについて知っておくべきこと〉
〈さらに読む: 液体射出成形(LIM)VS 圧縮成形;どちらがあなたに最適ですか? 〉
シリコーン射出成形とは何ですか?
シリコーン射出成形は、シリコーン製品を製造するための高効率な方法であり、シングルショット射出成形、インサート成形、ツーショット射出成形の3つのタイプがあります。このプロセスでは、液状のシリコーン原料を金型に注入し、高圧下で成形します。この技術は、製品の寸法と厚さを制御しながら複雑な幾何学的形状を成形できるため、高品質で高精度な製品の製造に広く使用されています。用途に応じてシリコーン射出成形の種類を選択することで、適切な製品を製造できます。
〈さらに読む:シリコーンゴムはどのように成形されるのか? 〉
シリコーン射出成形の種類
シリコーン射出成形には、シングルショット射出成形、インサート成形、ツーショット射出成形など、様々な種類があります。以下では、それぞれの特徴、メリット、デメリットを含め、それぞれの種類について詳しく説明します。
シングルショット注射
シングルショット射出成形とは、単一種類のシリコーン材料を用いて射出成形を行うことを指します。これは、シリコーン射出成形において最も一般的に使用されている方法です。この技術の最大の特徴は、成形速度が速いことです。これにより、高精度・高品質な製品を製造できます。また、単一材料射出成形機はメンテナンスと操作が比較的容易です。しかし、この方法には、使用する材料が単一であるため、多色または多硬度の製品を製造できないという制約があります。
液状シリコーンシングルショット射出成形法は、シリコーン製品の製造に用いられる特殊な射出成形技術です。この技術では、単一の液状シリコーン材料を使用し、複数の成分を混合する必要はありません。液状単材料射出成形法の一般的な手順は以下のとおりです。
材料の準備
適切な液状シリコーン材料を選択し、製品要件に応じて配合・調整します。材料の正確な調製と配合を確保します。
〈関連記事:スマート衣料における液状シリコーンゴム射出成形の応用〉
予熱
射出成形機のバレルの温度を 25 ℃ 未満に制御して、シリコン材料が金型にスムーズに流れ込み、適切に充填されるようにします。
型の準備
金型の洗浄や離型剤の塗布などの手順を含め、適切な金型を準備して、製品をスムーズに型から取り出せるようにします。
シリコーン射出成形
液状シリコーン材料(AB接着剤)をスタティックミキサーに注入し、射出成形機に移送します。射出成形工程では、材料が加熱された金型に注入されます。
〈関連記事:静電気防止シリコーン:静電気制御の鍵となる要素〉
金型充填
適切な射出圧力と速度を適用することで、液状シリコーンが金型キャビティ全体に充填されます。金型内のシリコーン材料の安定した流動を確保し、充填不良などの問題を防止するために、金型温度は均一に加熱する必要があります。
硬化
シリコンが型に充填されると、加熱された型内のシリコン材料が硬化し始めます。
脱型と後処理
十分な硬化時間の後、金型を開き、完成品を取り出します。製品の後処理には、エッジのトリミング、バリの除去、洗浄などが含まれます。
液状シリコーン単一材料射出成形プロセスは、操作の簡便さ、高い生産効率、製品品質の一貫性など、多くの利点を備えています。シール、ボタン、ハンドル、電子部品の封止など、様々な用途のシリコーン製品の製造に広く利用されています。
〈関連記事:液状シリコーンゴムのシール・ガスケットへの応用〉
インサート射出成形
インサートシリコーン射出成形とは、シリコーン製品の内部に金属やプラスチックなどの他の材料を注入することで、機能性や接続性を向上させるプロセスを指します。この技術の最大の特徴は、部品を埋め込みまたは接続したシリコーン製品を製造できることです。しかし、追加の材料を注入する必要があるため、インサート成形は単一材料射出成形に比べて一般的に成形時間が長くなり、コストも高くなります。
液状シリコーンインサート成形プロセスは、シリコーン製品内に他の材料や部品を埋め込むために一般的に使用される特殊なシリコーン成形技術です。液状シリコーンインサート成形プロセスの一般的な手順は以下のとおりです。
材料の準備
液状シリコーンと挿入する材料または部品を準備します。製品の要件に応じてシリコーンの配合と特性を調整します。
型の準備
シリコンパーツと材料を流し込むスペースを含む適切な型を準備します。型の表面が清潔であることを確認し、離型剤を塗布して型から容易に取り出せるようにします。
シリコン注入
液状シリコンを型に注入し、挿入する材料が完全に覆われるようにある程度まで満たします。
〈続きを読む:液状シリコーンゴム(LSR)の多様性と利点を知る〉
材料または部品の配置
挿入する材料や部品をシリコンに優しく置きます。位置と向きが正しいことを確認してください。
シリコン充填
埋め込まれる材料または部品が覆われるように、金型が完全に満たされるまで液体シリコンを注入し続けます。
〈続きを読む:舞台裏:バックライト付きシリコンキーパッド技術〉
硬化
シリコンの充填が完了すると、加熱された型内のシリコンが硬化し始めます。硬化時間はシリコンの特性と厚さによって異なります。
脱型と後処理
硬化後、金型を開いて完成品を取り出します。製品のエッジのトリミング、バリ取り、洗浄などの後処理を行います。
インサートシリコーン射出成形プロセスは、電子部品、プラスチック部品、金属部品、その他の材料をシリコーン製品に埋め込むことを可能にします。この技術は、電子機器、医療機器、自動車、消費財などの分野で広く利用されており、より幅広いデザインと機能性を提供します。
〈関連記事:自動車用途における液状シリコーンの将来〉
2ショット注射
2ショットシリコーン射出成形とは、2種類の異なるシリコーン材料を同時に射出成形に用いることで、複数の色や硬度の製品を製造する技術です。この技術の最大の特徴は、様々な色や硬度の製品を製造できることです。成形速度が速く、異なる物理的特性が求められる用途に適しています。ただし、専用の射出成形機が必要となるため、成形精度が低くなる可能性があり、機械のメンテナンスコストも高くなる可能性があります。
ツーショット射出成形は、シリコーン製品の製造に用いられる特殊なシリコーン射出成形技術であり、2種類の異なる液状シリコーン材料を用いて成形を行います。液状ツーショット射出成形の一般的な手順は以下のとおりです。
〈拡張読書:シリコーンの硬度についてより深く理解する〉
材料の準備
2種類の異なる液状シリコーン材料を準備し、製品要件に応じて配合を調整します。材料の正確な調製と配合を確保します。
予熱
射出成形機のバレル内の特定の低温を維持し、2 つのシリコン材料のスムーズな流れと充填を確保します。
型の準備
製品をスムーズに型から取り出せるように、洗浄や離型剤の塗布など適切な金型を準備します。
シリコーン射出成形
2種類の液状シリコーン材料を射出成形機の異なるバレルに注入します。射出工程中、それらは別々に冷却され、ノズルから金型内に注入されます。
〈関連資料:熱伝導性シリコーンゴムの理解:総合ガイド〉
金型充填
適切な射出圧力と速度を利用して、2 つの液体シリコン材料が金型の異なる領域に充填され、金型内の形状が正確に再現されるようにします。
硬化
2 つのシリコン材料が充填されると、加熱された型内のシリコンが硬化し始めます。
金型除去と後処理
十分な硬化時間の後、金型を開き、完成品を取り出します。製品のエッジのトリミング、バリの除去、洗浄などの後処理を行います。
デュアルショットシリコーン射出成形プロセスは、硬度、弾性、色、特性が異なるシリコーン製品の製造を可能にします。シール、ボタン、ハンドル、電子部品の封止など、多層構造や異なる性能領域を持つ製品が求められる用途で広く利用されています。このプロセスにより設計の柔軟性が向上し、より機能的で多様な製品の開発が可能になります。
〈続きを読む:ツーショット注射とインサート注射は同じですか? 〉
〈続きを読む:デュアルショット注射とは?その原理とメリットを理解する記事〉
シリコーン射出成形の比較
種類 | 特性 | 利点 | デメリット |
---|---|---|---|
シングルショットインジェクション | 単一タイプのシリコーンゴム | 射出速度が速く、成形精度が高く、メンテナンスが簡単です。 | 多色・多硬度の製品は製作できません。 |
挿入注入 | シリコンゴムに他の材料を注入する | インサートを作成する機能 | 成形時間が長くなり、コストが高くなります。 |
2ショット注射 | 2種類のシリコンゴムの同時使用 | 多色・多硬度の製品が生産可能で、成形速度も速い。 | 設備コストが高く、メンテナンスが複雑です。 |
シリコーン射出成形の 5 つの主な応用分野:
シリコーン射出成形は、医療、自動車、航空宇宙、電子機器、玩具など、様々な業界で広く利用されています。以下に、これらの業界のいくつかについて詳しく説明します。
応用分野1:医療業界
シリコーン射出成形は医療業界で広く利用されており、手術用手袋や人工呼吸器などの高品質な医療機器や器具を製造できます。シリコーン自体は優れた生体適合性を持つ素材であるため、シリコーン製の器具はアレルギーやその他の副作用を引き起こす可能性が低くなります。また、シリコーンは耐摩耗性と耐腐食性にも優れており、消毒や滅菌などの一般的な洗浄方法にも耐えることができます。さらに、シリコーン素材の柔軟性と弾力性は、手袋やその他の器具の快適性と安全性に貢献します。
〈関連記事:医療グレードシリコーン:それをどう定義するか? 〉
応用分野2:自動車産業
シリコーン射出成形技術は自動車産業でも広く応用されており、車のライト、ダッシュボード、エアデフレクター、ホースといった優れた自動車部品の製造に用いられています。シリコーンは耐熱性と耐摩耗性に優れていることで知られており、自動車部品の製造に最適です。さらに、シリコーン材料は優れた耐候性と化学的安定性を備えており、紫外線や様々な化学的腐食にも耐え、自動車部品の寿命を延ばします。
〈関連記事:シリコーン業界がネットゼロ炭素排出目標を達成する方法〉
応用分野3:航空宇宙産業
シリコーン射出成形技術は航空宇宙産業で広く利用されており、高精度で複雑な部品の製造で知られています。例えば、航空機のエンジンや翼部品には高品質で信頼性の高い材料が求められるため、シリコーン射出成形は理想的な選択肢です。この技術により、複雑な設計要件を満たすと同時に、優れた耐久性と耐疲労性を備えた部品の製造が可能になります。これらの部品は、高高度、低温、高圧といった過酷な条件にも耐えることができます。
応用分野4:電子産業
シリコーン射出成形技術は、優れた保護性能と防水性能を備えた製品を製造できるため、エレクトロニクス業界で広く利用されています。例えば、携帯電話ケースやバッテリーケースなどの製品では、内部回路やバッテリーを保護すると同時に、寿命と安全性を高めるために防水性も求められます。シリコーン射出成形は、これらの要件を満たす製品を製造し、柔軟性と弾力性を与えることで、製品の快適性と耐久性を向上させます。
〈関連記事:シリコーンゴムOEMメーカー – Glory Sun Group 〉
応用分野5:玩具産業
最後に、一部の玩具製品にはシリコーン射出成形が使用されています。シリコーンは柔らかく弾力性のあるため、バービー人形、ベビー玩具、ケア用品など、多くの小型玩具に適しています。シリコーン射出成形は、これらの要件を満たすだけでなく、優れた安全性と耐久性も備えた玩具を製造できるため、玩具を安全に長くお使いいただけます。
〈関連記事:シリコーンは有毒か?シリコーンの安全性に関する包括的分析〉
シリコーン射出成形における一般的な問題
シリコン射出成形の利点は何ですか?
シリコーン射出成形技術には、生産速度の速さ、高精度、生産効率の高さ、製品品質の安定性など、さまざまな利点があります。シリコーン射出成形には、次のような利点があります。
設計の柔軟性
シリコーン射出成形は、細長い構造、薄肉部品、微細構造など、複雑な形状の製品を製造できます。この技術は、寸法と細部において高い精度を実現し、従来の成形方法では実現が困難な製品の製造を可能にします。
〈関連記事:導電性シリコンストリップ:効率的な導電性ソリューションの理想的な選択肢〉
高品質と一貫性
シリコーン射出成形プロセスでは、材料が金型キャビティ内に均一に充填され、硬化プロセスを通じて一貫した寸法と性能を維持します。これにより、高品質で一貫性があり、信頼性の高い製品が保証されます。
材料特性
シリコーンゴムは、優れた弾性、耐高温性、耐薬品性、絶縁性など、優れた特性を備えています。シリコーン射出成形によりこれらの特性を維持できるため、幅広い用途に適した製品となっています。
〈関連資料:高温シリコーン:特性、用途、購入ガイド〉
高い生産効率
シリコーン射出成形は、迅速な生産という利点があります。金型設計が完成し、検証されると、生産プロセスを高度に自動化できるため、継続的かつ効率的な生産が可能になります。これにより、生産効率が向上し、コストが削減されます。
〈続きを読む: TPEとシリコーンゴム、どちらを選ぶ?それぞれの特徴を知ろう! 〉
柔軟性とデザインの自由度
シリコーン射出成形は、柔軟な製品設計と迅速な製品開発を可能にします。設計者は、製品の形状、サイズ、硬度、色などの特性をニーズに合わせて調整できるため、顧客のさまざまな要件を満たすことができます。これにより、設計の自由度が向上し、カスタマイズの選択肢が広がります。
まとめると、シリコーン射出成形は、複雑な形状を製造できる能力、高品質、優れた材料特性、高い生産効率、そして優れた柔軟性といった利点を備えています。これらの利点により、電子機器、医療、自動車、消費財など、幅広い産業分野における用途に最適な選択肢となっています。
シリコン射出成形で使用される一般的なシリコン材料は何ですか?
シリコーン射出成形に使用される一般的なシリコーン材料には、シリコーンゴム、メチルシリコーンゴム、ブチルシリコーンゴムなどがあります。
〈続きを読む:一般的なエラストマーシリコンとは?見逃せないヒントはこちら〉
一般的なシリコーンゴム
標準シリコーンとも呼ばれ、様々な製品に広く使用されています。優れた弾力性、柔軟性、耐高温性を備えています。一般的なシリコーンは、様々な用途の要件に対応するために、通常、様々な硬度の製品が提供されています。
〈続きを読む: シリコンゴムはゴムより優れているのか? 〉
高透明シリコンゴム
このタイプのシリコーンゴムは、非常に高い透明性と光学特性を示し、照明製品、光学部品など、透明または半透明の効果が必要な製品に適しています。
難燃性シリコンゴム
このタイプのシリコーンゴムは優れた難燃性を有し、高温下でも炎の広がりを抑制します。難燃性が求められる電子製品や自動車部品などに広く使用されています。
医療グレードのシリコンゴム
このタイプのシリコーンゴムは、高い生体適合性と医療安全性を備え、医療機器に関する関連規格および要件に準拠しています。医療グレードのシリコーンは、カテーテル、人工臓器、医薬品保存容器など、医療機器や製品に広く使用されています。
〈関連記事:導電性シリコーンゴムとは?シリコーンと導電性から学ぶ! 〉
高強度シリコンゴム
このタイプのシリコーンは、引張強度と引裂強度が高く、自動車用シール、工業用部品など、優れた機械的性能が求められる用途に適しています。
上記のシリコーンゴムのオプションは、シリコーン射出成形で使用される一般的なタイプのほんの一部です。特定の用途要件に応じて、他の特殊な配合やカスタマイズされたシリコーンゴムもご用意しております。
シリコーン射出成形で色の多様性を実現するにはどうすればよいでしょうか?
色の多様性を実現するには、異なるシリコーン材料と着色添加剤を使用する必要があります。比率と組み合わせを調整することで、さまざまな色の製品を作ることができます。
シリコン射出成形では、主に以下の方法で色の多様性を実現できます。
顔料を加える
シリコーン材料に顔料を添加することは、色の多様性を実現するための一般的な方法です。顔料は固体粉末または液体の形態で、シリコーンゴムと混合することで、様々な色のシリコーン材料を得ることができます。この方法により、幅広い色の選択肢が得られます。
〈関連記事:ソリッドシリコンHTVとは〉
染色剤
シリコーンゴムの色を変えるには、顔料の添加に加えて、染色剤を使用することもできます。染料はシリコーン分子と相互作用し、所望の色を与えます。この方法は、特定の領域を識別したり、医療機器の色を区別したりする必要があるなど、特殊な用途でよく使用されます。
〈関連記事: 医療機器における液状シリコーンゴムの応用〉
印刷とスプレー
複雑な模様や特殊効果が必要な製品では、印刷やスプレー技術を用いてシリコン表面に色を付けることが可能です。これは、塗料のスプレー、印刷技術、または特殊な着色処理を施すことで実現できます。
色の混合
シリコーン射出成形工程では、異なる色のシリコーン材料を混合することで、色彩混合効果を得ることができます。この方法により、グラデーションカラー、色彩変化、あるいは多色混合といった効果が得られます。ただし、シリコーン材料の透明性も最終的な演色効果に影響を与えることに注意が必要です。
透明または半透明のシリコン製品の場合、色が薄く見えたり、わずかに透明に見えたりすることがあります。全体的に、シリコン射出成形では、さまざまな用途の色要件を満たすさまざまな色を実現できます。
〈続きを読む:環境に優しいシリコーンとは?その4つの主な素材メリットと用途を分析! 〉
結論
シリコーン射出成形は、様々な射出成形方法に対応できる、広く使用されている成形技術です。生産速度の速さ、高い生産精度、柔軟な設計、優れた材料性能を特徴とし、様々な業界で広く応用されています。シリコーン製品にご興味をお持ちでしたら、Glory Sun Group の製造サービスをぜひご検討ください。当社はカスタムシリコーン製品のリーディングメーカーとして、関連する専門サービスを提供しています。高品質な製品を製造するだけでなく、合理化され効率的なサービスプロセスを重視しており、これも当社の大きな特徴です。ご要望がございましたら、お気軽にお問い合わせください。
〈続きを読む: シリコーンゴムサプライヤーを選ぶための4つのヒント〉