BLOG
- Home
- Blog
- Silicone Rubber Introduction
- How to choose between TPE and Silicone Rubber? Find out their respective characteristics!
How to choose between TPE and Silicone Rubber? Find out their respective characteristics!
April 17,2023
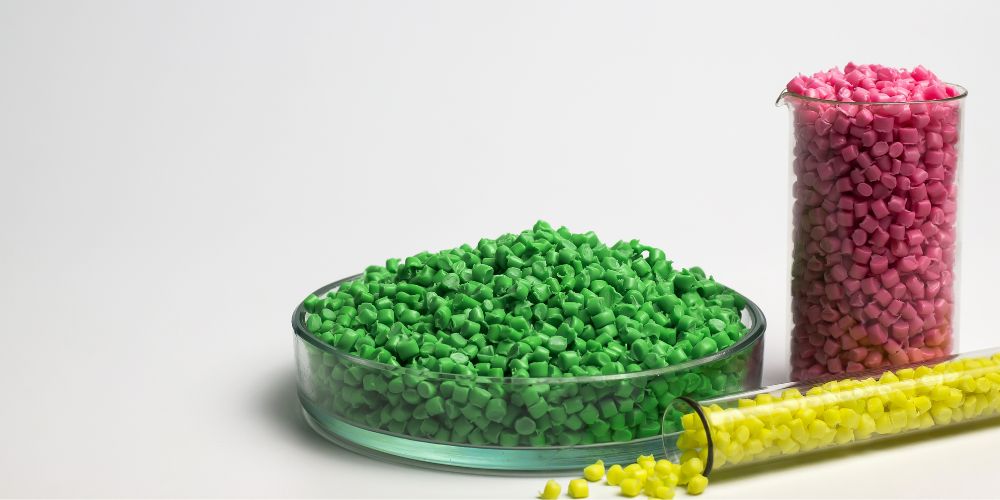
How to know if TPE or Silicone rubber is more ideal? TPE information jumps out always when we are searching for the silicone material, which will inevitably make people compare them together. What exactly are the differences between TPE and Silicone rubber? Let me briefly explain from three aspects to help you understand:
Application: TPE and silicone rubber have different characteristics such as elasticity, temperature resistance, wear resistance, etc., and their applicable range is not entirely the same.
Silicone rubber is a synthetic polymer composed of natural elements such as silicon, oxygen, carbon, and hydrogen. It can be classified into one-component and two-component types and is widely used in processing due to its stable chemical properties.
How should I choose between TPE and silicone rubber? Let's simplify it by summarizing the common application ranges for both materials:
<Extension: How to distinguish food-grade silicone and regular silicone? >
<Extension: Medical Grade Silicone: How to define it? >
<Extension: What is zebra elastomeric connectors? Learn it from silicone and conductivity! >
Interested in learning more about the applications of silicone rubber?
<Extension: What is the common elastomeric silicone? here is some tips you can't miss out>
If your product requires high temperature resistance, wear resistance, and chemical resistance, silicone rubber is a better choice. This is often seen in applications such as medical devices and automotive components.
On the other hand, if your product emphasizes high elasticity, flexibility, and good processing capabilities, TPE is a better option. This is commonly seen in household products and sporting goods, etc.
Regardless of whether you choose TPE or silicone rubber, it's crucial to select a reliable manufacturing partner to ensure the material and production quality.
We not only have over 30 years of experience in silicone rubber production, but also qualified by international certificates such as SGS, RoHS, REACH, and FDA, offering four key advantages:
Glory Sun Group has rich experience and technology in the field of silicone rubber manufacturing. We possess advanced production equipment and technique, a strict quality control system, and a comprehensive after-sales service system. We are committed to providing high-quality, efficient, and customized product manufacturing services to our customers. If you have any TPE or silicone rubber production needs, please click here to contact us.
Application: TPE and silicone rubber have different characteristics such as elasticity, temperature resistance, wear resistance, etc., and their applicable range is not entirely the same.
- Safety: If the product will come into contact with the human body, material safety should be considered. Silicone rubber is generally considered safe, while the safety of TPE depends on its composition.
- Cost: TPE is cheaper than silicone rubber. If cost is a factor to consider, then TPE can be a viable option.
What are the differences between TPE and silicone rubber?
TPE (Thermoplastic Elastomers) is a highly elastic, flexible, and durable synthetic material that combines the flexibility of rubber with the plasticity of plastic. Silicone, also known as silicone rubber, is a polymer material primarily composed of silicon (Si), oxygen (O), and other elements. Both materials are highly elastic, and here we will briefly summarize their differences for you:- Characteristics: TPE has great elasticity and elastic recovery, however, compared to it, silicone rubber has higher performance. TPE has better wear and oil resistance, whereas silicone performs better in high-temperature resistance.
- Safety: Silicone rubber is considered safer because its composition is purer, while the safety of TPE depends on its composition.
TPE :Thermoplastic Elastomers
TPE is a copolymer formed by blending hard blocks (typically plastic) and soft blocks (typically rubber), creating a network structure with a conjugated configuration. It can be processed using plastic manufacturing techniques such as injection molding, extrusion, and blow molding, and it possesses high elasticity and flexibility.- Softness: TPE has excellent softness, typically ranging from Shore A hardness 0 to 100A.
- Tensile Strength: also known as tensile strength, for TPE typically falls within the range of 200% to 1500%.
- Temperature resistance: -35~80°C
- Odor: TPE contains carbon elements and can easily absorb smell. Recycled TPE may have a higher tendency to retain odors as well.
- Material Aging: TPE is prone to faster material aging.
Silicone Rubber: Thermoset Elastomer
Silicone rubber is a synthetic polymer composed of natural elements such as silicon, oxygen, carbon, and hydrogen. It can be classified into one-component and two-component types and is widely used in processing due to its stable chemical properties.
- Softness: Due to slight toughness in its softness, silicone rubber is not as soft as TPE. It typically ranges from Shore A hardness 30A to 70A.
- Tensile Strength:90~1120%
- Temperature tolerance: -40~220°C
- Odor: Odor: High inertness, not easily adsorbing smell, odorless.
- Material Aging: High inertness, slow material aging speed.
TPE | Silicone rubber | |
---|---|---|
Production Method | co-polymerized from soft and hard blocks | Vulcanization and heat molding. |
Production Cost | Lower | Higher |
Softness | Softer | slight toughness in softness |
Tensile Strength | High | Low |
Temperature tolerance | -35~80°C | -40~220° |
Odor | More prone to have odors. | Less likely to have odors. |
Material Aging | Fast aging speed | Low aging speed |
How to choose between TPE and silicone rubber from the application perspective?
How should I choose between TPE and silicone rubber? Let's simplify it by summarizing the common application ranges for both materials:
- Medical Products: Silicone rubber is more suitable for use in medical products such as surgical instruments, prosthetics, and implants. This is because silicone rubber exhibits biocompatibility and does not elicit adverse reactions in the human body.
- Baby Products: Due to the delicate nature of infant skin, it is essential to use safe materials. Silicone rubber is a safe and durable choice for baby products such as baby bottles, pacifiers, and teething toys.
- Automotive Parts: Automotive parts require good wear resistance and aging resistance. Therefore, TPE is a preferable choice for components such as window seals, door gaskets, and other automotive seals.
- Home Appliances: Home appliances require heat resistance, making silicone rubber a better choice for items such as oven mats, baking mats, and grill mats.
TPE
TPE (Thermoplastic Elastomer) offers excellent elasticity, flexibility, and processing capabilities, making it a preferred material for designers and manufacturers. As a result, it has a wide range of applications in various fields. Here are some common application areas for TPE:Automotive Industry
TPE is commonly used in the automotive industry for manufacturing vehicle components, with widespread applications including door seals, window seals, wheel covers.Sports Equipment
TPE, with its lightweight, abrasion-resistant, and non-slip characteristics, has gained great popularity in the field of sports equipment. It can be used in various applications, including sports shoe soles, fitness equipment mats, and more.Medical Devices
Due to its good biocompatibility, TPE is widely used in various medical products, including gloves, assistive devices, blood pressure cuff, catheters, and other medical supplies.Household Products
TPE's excellent flexibility, comfort, and low cost make it widely used in various everyday household items, such as chair cushions, insoles, floor mats, sofa covers.Packaging Materials
TPE is cost-effective and allows for quick and large-scale production, making it highly suitable for packaging materials such as bottle caps, food packaging, cosmetics packaging, etc.3C Products
TPE exhibits excellent wear resistance, shockproof, and protective function, making it suitable for manufacturing various 3C (Computer, Communication, and Consumer electronics) products. It can be used for making mobile phone cases, outer protective sleeves for charging/data cables, tablet cases, headphone cables, etc.Building Materials
In addition to its application in automotive seals, TPE can also be found in building materials such as sealing strips. Furthermore, it can be used in soundproofing strips, waterproof materials, and other applications to enhance the sealing and weather resistance of buildings.Silicone rubber
Silicone rubber offers excellent performance and durability, which leads to its wide-ranging applications across various industries. Here are some specific application areas:Eating/Kitchen Utensils
Silicone rubber is known for its excellent heat resistance and non-toxicity, making it widely used in food-related products. Common applications include kitchen utensils (such as silicone baking mats, silicone baking molds, silicone spatulas), silicone tableware, silicone seasoning bottles, silicone oven gloves, silicone food storage bags, sealing lids, and silicone coasters, etc.<Extension: How to distinguish food-grade silicone and regular silicone? >
Medical
Silicone rubber possesses excellent biocompatibility and antibacterial properties, which contribute to its widespread use in medical products. Applications include surgical instruments, medical devices (such as pacemaker leads, catheters, endotracheal tubes), artificial organs, medical tubing, and implants (like artificial joints, breast implants), etc.<Extension: Medical Grade Silicone: How to define it? >
Baby/Infant Products
Silicone rubber's excellent stability makes it a common choice for highly safety-conscious baby and infant products such as baby bottles, pacifiers, teething toys, etc.Electrical Products
Silicone rubber is used in electrical products primarily as insulation and sealing materials. For instance, it is used to manufacture insulation sheaths for wires and cables, as well as sealing components for electrical switches. Additionally, silicone rubber serves as an excellent bridge for electronic components, making it extensively applied in the LED industry.<Extension: What is zebra elastomeric connectors? Learn it from silicone and conductivity! >
Architecture
Silicone rubber is mainly used as a sealant and joint material in the construction industry. Silicone sealants offer excellent weather resistance, aging resistance, and temperature resistance, making them commonly used for sealing glass curtain walls, doors and windows, pipes, and other building components.Electronics and Telecommunications
Silicone rubber provides good mechanical protection, waterproofing performance, and heat resistance. Its applications in the electronics and telecommunications industry include mobile phone cases, fixation and insulation of electronic components, and sealing of wires and connectors.Aviation
Silicone rubber is mainly used in the aviation industry as a sealant, insulation material, and lubricant. For example, high-performance silicone sealants are required in aircraft engine components, fuel systems, hydraulic systems, and other areas to ensure sealing effectivity.Green Energy
Silicone rubber plays a crucial role as a sealant and insulation material in the solar energy and wind energy industries. For instance, solar panels require silicone sealants to protect the solar cells and glass, ensuring weather resistance and durability. Similarly, silicone sealants are used to seal and protect components of wind turbines.Automotive Parts
Certainly, silicone rubber can be used in the automotive industry as well. Common silicone products in this industry include silicone seal strips, silicone wheel covers, and silicone suspension materials.Industrial Applications
Silicone rubber's excellent durability makes it highly suitable for industrial applications as well. Common finished products include silicone hoses, silicone seals, and silicone oil seals, etc.Interested in learning more about the applications of silicone rubber?
<Extension: What is the common elastomeric silicone? here is some tips you can't miss out>
Recommendations for silicone rubber manufacturing|Glory Sun Group
Silicone rubber and TPE are both excellent polymer materials suitable for various product applications. To determine which material is better for your needs, we would recommend you to consider from the perspective of specific application and requirements of the product.If your product requires high temperature resistance, wear resistance, and chemical resistance, silicone rubber is a better choice. This is often seen in applications such as medical devices and automotive components.
On the other hand, if your product emphasizes high elasticity, flexibility, and good processing capabilities, TPE is a better option. This is commonly seen in household products and sporting goods, etc.
Regardless of whether you choose TPE or silicone rubber, it's crucial to select a reliable manufacturing partner to ensure the material and production quality.
We not only have over 30 years of experience in silicone rubber production, but also qualified by international certificates such as SGS, RoHS, REACH, and FDA, offering four key advantages:
- Rich Experience and Technology: Glory Sun Group has years of experience in silicone rubber manufacturing and possesses rich production technology and management experience. Additionally, Glory Sun Group has achieved a series of accomplishments in the research and application of silicone rubber materials, enabling us to provide customers with more professional technical support.
- Advanced Production Equipment and Technique: Glory Sun Group possesses multiple advanced silicone rubber injection molding production lines and professional production technique which leads us to meet various production requirements from customers as well as ensuring product quality and delivery schedule.
- Strict Quality Control System: Glory Sun Group implements strict quality control measures throughout the silicone rubber manufacturing process. From raw material inspection and production processes to finished product release, we conduct rigorous testing in accordance with international standards to ensure that our products meet customer requirements and standards.
- Comprehensive After-Sales Service System: Glory Sun Group provides a complete after-sales service system, allowing us to promptly adjust product production and service in response to customer needs. We strive to ensure customer satisfaction and maintain long-term cooperative relationships.
Glory Sun Group has rich experience and technology in the field of silicone rubber manufacturing. We possess advanced production equipment and technique, a strict quality control system, and a comprehensive after-sales service system. We are committed to providing high-quality, efficient, and customized product manufacturing services to our customers. If you have any TPE or silicone rubber production needs, please click here to contact us.