- Home
- Blog
- Liquid Silicone Rubber
- What is dual-shot injection? An article understanding its principles and advantages
What is dual-shot injection? An article understanding its principles and advantages
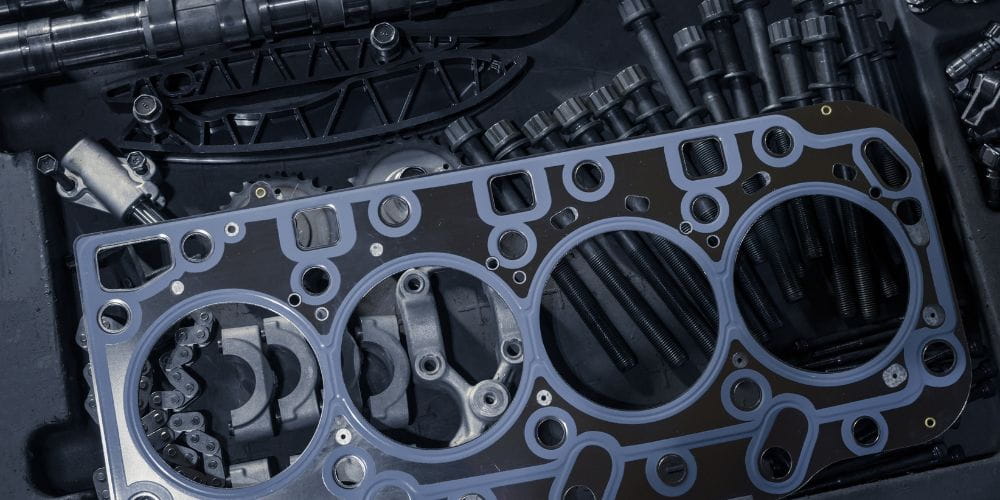
Are you aware that double injection molding technology is actually prevalent in our daily lives? It can be found in various products such as two-tone toothbrushes, electrical wires, vehicle components, and more. If you want to make your own products more competitive in the market, it's important to understand the benefits of double injection molding. This technology can enhance product aesthetics, improve performance, optimize production processes, and reduce manufacturing costs and waste. Let's explore how double injection molding can provide consumers with a better user experience!
What is double injection?
Double injection molding, also known as two-shot injection molding or two-color injection molding, is a technique used in injection molding. The principle involves loading two different plastic materials into the injection cylinder of a single injection machine. Through the injection system of the machine, the two different plastic materials are injected into the mold simultaneously or alternately, forming a product with two different colors or materials. In simple terms, double injection molding uses a single injection machine to produce plastic products with two different colors or materials in a single mold, achieving the purpose of two-color injection molding or mixed injection molding. Double injection molding typically requires the use of special mold designs, including moving plates and rotating plates, to ensure precise control over the injection position and timing of the plastic materials in the mold. Additionally, the production principles of double injection molding can vary depending on the specific technique types. Let's take a look at the four common types of double-shot injection molding techniques available in the market!
Sequential Injection
In this technique, the first material is injected into the mold cavity, and after it solidifies partially, the second material is injected to form the final part. The two materials are injected sequentially, one after the other, in a specific order.
Advantage
- Design Flexibility: Sequential Injection allows for more intricate and complex designs by precisely controlling the placement of different materials within the mold cavity. This technique enables the creation of parts with varying colors, textures, or material properties in specific areas, enhancing the overall aesthetics and functionality of the product.
- Improved Bonding: By injecting the first material and allowing it to partially solidify before injecting the second material, Sequential Injection ensures better bonding between the two materials. This results in a stronger and more durable final part, as the two materials effectively fuse together during the molding process.
- Enhanced Material Compatibility: Sequential Injection enables the use of different materials with varying properties in a single part. This is particularly advantageous when combining materials with incompatible melting temperatures or chemical compositions. By injecting each material separately, manufacturers can select the most suitable materials for specific regions of the part, optimizing its performance.
Application
- Products need to come in many different colors.
- The production volume of two-color injection molding products is large and the production cycle is short.
Rotary Platen
This technique involves the use of a rotary platen that rotates the mold between the two injection shots. The first material is injected into one side of the mold, the platen rotates, and then the second material is injected into the other side of the mold. This method allows for efficient production of two-color or two-material parts.
Advantage
- Efficient Production: The Rotary Platen technique allows for simultaneous injection of two different materials or colors into the mold. This results in a faster production process compared to other dual-shot techniques that require separate molding cycles for each material. The rotational movement of the platen enables the injection of the second material while the first material is solidifying, reducing overall cycle time.
- Consistent Alignment: With the Rotary Platen technique, the mold rotates between the two injection shots. This rotational movement ensures precise alignment of the two materials, resulting in accurate and consistent placement of the second material relative to the first material. This helps to maintain design integrity and avoid misalignment issues that can occur in other techniques.
- Simplified Tooling: The Rotary Platen technique typically uses a single mold with two cavities or sides, where each side corresponds to one material. This simplifies tooling compared to other techniques that may require more complex mold designs or additional tooling components. The simplified tooling reduces manufacturing complexity and cost.
Application
- necessary to manufacture products with complex dimensions, such as: automotive interior parts, industrial machine parts, home appliances...etc.
- Products with high requirements on product surface quality and appearance, such as mobile phone casings, electronic product casings...etc.
Core back
Core back technique involves using a movable core in the mold. The first material is injected around the core, and then the core is retracted, creating a void. The second material is then injected into the void, surrounding the first material. This technique is commonly used for creating parts with overmolding or encapsulation.
Advantage
- Overmolding Capabilities: The Core Back technique allows for the overmolding of one material onto another. This enables the creation of parts with a soft or flexible material encapsulating a rigid or structural material. The resulting part exhibits improved functionality, enhanced grip, vibration dampening, and improved sealing properties. Overmolding can also provide added protection, cushioning, or aesthetic appeal to the final product.
- Enhanced Design Possibilities: With Core Back, manufacturers have the flexibility to design parts with intricate shapes or complex geometries that incorporate different materials. The technique enables the creation of parts with varying colors, textures, or material properties in specific areas, opening up new design possibilities and allowing for customized solutions.
- Improved Product Performance: The Core Back technique allows for the precise placement of different materials within the part, optimizing its functionality. By strategically selecting materials with specific properties, manufacturers can enhance features such as grip, cushioning, insulation, chemical resistance, or wear resistance, improving the overall performance of the final product.
Application
- Suitable for small and medium batch production or scenarios with high product value, because the injection molding cycle is longer and the manufacturing cost of the mold is higher.
- Requires high-quality products such as high-precision appearance, distinct colors, and clear textures.
Spin Stack
Spin stack technique utilizes a rotating stack mold. The first shot is injected into the stationary part of the mold, and then the mold rotates, allowing the second shot to be injected onto the previously injected material. This technique is suitable for producing complex parts with multiple materials or colors.
Advantage
- Complex Design Capabilities: Spin Stack enables the production of intricate parts with complex designs and geometries. The rotating stack mold allows for precise placement of different materials or colors in specific areas of the part. This technique offers design freedom to create visually appealing and functionally optimized products.
- Versatile Material Combinations: The Spin Stack technique allows for the combination of different materials with distinct properties in a single part. This enables manufacturers to leverage the strengths of each material, such as rigidity, flexibility, or different textures, to enhance the overall performance and functionality of the final product.
- Reduced Assembly and Post-Processing: By incorporating multiple materials or colors in a single molding process, Spin Stack eliminates the need for additional assembly or post-processing steps. This simplifies the production process, reduces labor costs, and improves overall manufacturing efficiency.
Application
- Suitable for large-scale two-color injection molding plastic parts.
- It is necessary to manufacture products with special shapes, such as products with various shapes such as protrusions and depressions.
- It is necessary to manufacture products with complex structures of more than two plastic materials, such as plastic gears, screw caps, etc.
overall pros and cons of four types of double injection molding:
Sequential Injection | Rotary Platen | Core Back | Spin Stack | |
---|---|---|---|---|
Pros | Cost efficiency | The process is simple and easy to control,product quality is higher | Design flexibility for complex parts | Complex design capabilities for intricate parts, Versatile |
Cons | Requires precise control and coordination of material injection | Requires a rotary platen and specialized equipment | Requires a movable core and additional tooling components, cost higher | Requires a rotating stack mold and specialized equipment, cost highest |
applicable scenarios | mass production with simple structure product | complex products with precise dimensions of production | multiple colors or materials production | Medium to large size of products that are intricate |
The advantage of Double injection
Double injection offers several advantages that can enhance product competitiveness:
1. Expanded Design Possibilities:
With dual-shot injection, complex designs, multi-color patterns, and multi-material parts can be created in a single molding process. This eliminates the need for assembly or post-processing steps and allows for seamless integration of different materials, colors, or textures in a single component.
2. Enhanced Functionality:
By combining different materials with distinct properties, dual-shot injection enables the production of parts with improved functionality. For example, a rigid base combined with a soft grip can enhance the ergonomics and user experience of a product.
3. Cost and Time Efficiency:
Dual-shot injection eliminates the need for additional assembly or post-processing steps, reducing production time and costs associated with labor, inventory, and equipment. This streamlined process improves overall efficiency.
4. Increased Durability:
The integration of different materials through dual-shot injection can enhance the durability and strength of the final product. By combining materials with complementary properties, such as rigidity and flexibility, the part can withstand varying stresses and strains, resulting in a longer lifespan.
5. Reduced Waste and Environmental Impact:
Dual-shot injection minimizes material waste compared to traditional manufacturing methods involving separate production and assembly steps. Additionally, it allows for the use of recycled materials or sustainable alternatives, contributing to a more environmentally friendly production approach.
In summary, Double injection enables unique design possibilities, improved functionality, cost and time efficiency, increased durability, and reduced waste. Leveraging these advantages can enhance product competitiveness and meet the evolving demands of the market.
Common applications of double injection:
Double injection technology is an injection molding technology widely used in various industries. It can inject different materials into the same mold and produce high-quality products. Several common application areas will be introduced below.
Household Appliances
Double injection molding is used for producing parts in household appliances like kitchen gadgets, vacuum cleaners, and personal care devices. It enables the integration of materials with different textures or colors to enhance aesthetics and ergonomics.
Consumer Electronics
Double injection molding finds application in consumer electronics for producing parts like mobile phone casings, remote controls, computer keyboards, and game controllers. It enables the combination of materials with different properties, such as rigid and soft-touch surfaces, or transparent and opaque sections.
Automotive Industry
Double injection molding is widely used in the automotive industry for producing parts such as interior trim components, buttons, knobs, handles, and instrument panels. It allows for the integration of different materials and colors in a single part, enhancing the visual appeal and functionality of automotive interiors.
Medical Devices
Double injection molding is utilized in the medical device industry to create parts with specialized features. It allows for the integration of materials with varying characteristics, such as antimicrobial surfaces, soft-touch grips, or transparent windows for visibility.
Top choice for double injection molding manufacturer【GSUN】.
Double injection molding technology has become an indispensable and important technique in modern production, widely applied in various industries' manufacturing processes. GSUN Group offers professional double injection molding services. The entire factory is certified with ISO 9001, ISO 14001, ISO 13485, and IATF 16949 international standards. From mold manufacturing to shipping and quality verification, we adhere to regulatory-compliant production management. We utilize the best instruments throughout the entire process to develop double injection molded products. Regardless of your industry, GSUN Group can provide the most reliable and competitive products using double injection molding technology. Feel free to contact us for further consultation.
Article Classification
Recent Articles
- Applications of Liquid Silicone Rubber Injection Molding in smart clothing
- Discover the Versatility and Benefits of Liquid Silicone Rubber (LSR)
- The Application of Liquid Silicone Rubber in Seals and Gaskets
- Applications of Liquid Silicone Rubber in Medical Devices
- The Future of Liquid Silicone in Automotive Applications