- Home
- Blog
- Liquid Silicone Rubber
- Is Two Shot Injection same as Insert Injection?
Is Two Shot Injection same as Insert Injection?
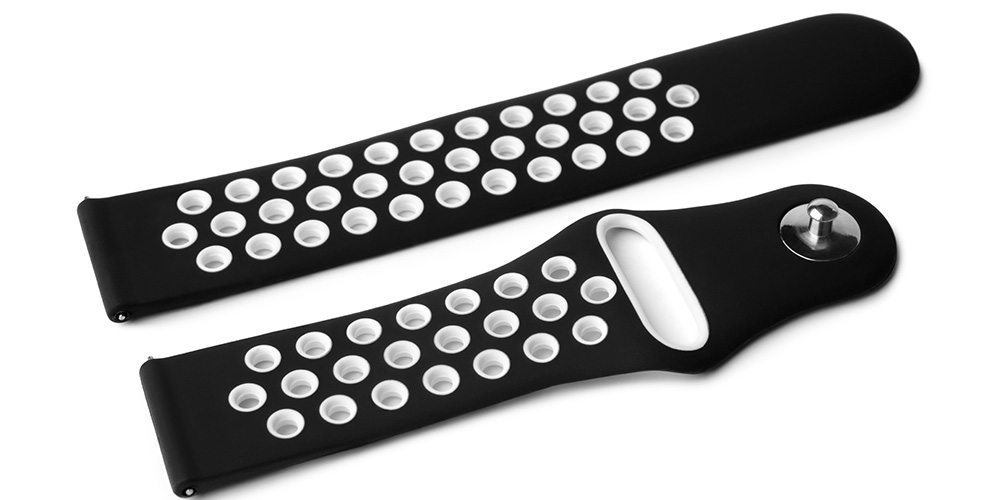
The non-toxic and environmentally friendly characteristics of liquid silicone are used in the field of injection molding. Whether it is a silicone kettle combined with metal, goggles combined with rubber and plastic, etc., liquid silicone is ubiquitous in life, and most of them are composite products that coexist with other materials. It can be made by insert injection or 2-shot injection. What is insert injection, and what is 2-shot injection? What is the relationship between these processing methods and liquid silicone products? Let's take a look at the foundry process of liquid silicone implantation and injection, and choose the most suitable foundry manufacturer for you.
Is Insert Injection same as 2-hot Injection?
The concept of insert injection and 2-shot injection is the same, but the production process is slightly different. To put it simply, it is to combine two or more materials. Usually, relatively hard metals and plastics are used as skeletons or parts, and soft rubber and silicone materials are injected to cover them. For example: Kitchenware or hardware with silicone handles are common examples. The difference between insert injection and 2-shot injection is that 2-shot molding can inject more than two materials in one process, while insert injection can only inject a single material. These characteristics also reflect their respective advantages. 2-shot injection is suitable for the production of multi-color and multi-material products, and the insert injection is suitable for mass production of less complicated products.
〈Extension Reading:What is Two Shot Molding?〉
The advantage of liquid silicone rubber
Anti-slip and smooth touch
Compared with metals and some rubbers and plastics, silicone rubber is a material with good elasticity, waterproof, acid and alkali resistance, and high skin-friendliness. Coating the outside of metals and rubbers and plastics can block foreign objects and prolong the product life, while improving user experience. In addition, liquid silicone rubber has the advantages of no added vulcanizing agent and high cleanliness in the production process, so it is often used in contact or implantable products, such as food-grade or even medical-grade products, such as pacifiers, silicone delivery tubes.
〈Extension Reading:What is the common elastomeric silicone? here is some tips you can't miss out〉
Wide range of applications
Although the texture of liquid silicone rubber is soft, the physical properties such as elasticity and hardness can be adjusted by adjusting the proportion of raw materials. For example, it can produce pacifiers with a hardness(Shore A) of 20A, and silicone shoe boards with a hardness of 80A. In addition to the medical and food industries mentioned above, liquid silicone has a wide range of applications. The advantages of waterproof and acid and alkali resistance are very suitable for use in automotive parts. The characteristics of cold resistance to -100 ° C also make it play a key role in the aerospace industry. , At the same time, its electrical insulation is also very suitable for the production of electronic parts. Liquid silicone is a material with high plasticity.
〈Extension Reading:How liquid silicone rubber work on your demands?〉
EU environmental standards conformity
Rubber and plastic are cheaper than silicone rubber. The disadvantage is that it can be toxic if used improperly. In contrast, liquid silicone rubber is clearly defined as a green and environmentally friendly material that does not contain phthalic acids that affect reproduction and development, and halogens that harm the respiratory and nervous systems. The Restriction of Chemical Substances Regulations (REACH) and other related regulations are in line with the environmental protection standards of highly developed countries, and are also solutions for enterprises to pursue environmental protection and sustainability in recent years.
Process of insert injection molding
1.The surface of the coated parts should be clean
Since the melting point of liquid silicone rubber(LSR) is around 130 degrees, the co-injection part needs to be higher than the melting point to avoid damaging the finished product. The surface of the co-injection part needs to be kept clean to ensure the quality of the finished product.
2.Prime the surface of the coating part
The primer is a kind of paint that makes the injection material and the lagging part adhere tightly, so before embedding the injection, it is necessary to brush a layer of primer on the surface of the lagging part. This step also pays attention to precise application, eliminating the need to remove residual glue afterwards.
3.Bake lagging parts
After the primer is applied, the lagged parts are dried in an oven while allowing the two to react chemically at the right temperature.
4.Put the lagging part into the mold for injection
Put the lagging part in the slot of the mold and start injection molding. Manufacturers equipped with automated equipment don't even need to manually install the lagging part.
5.Burr(flash)removing
The finished product will inevitably have fine burrs, and the burrs should be cleaned to ensure the fineness of the size of the product. This step is done manually, so proper mold design can make this a lot easier.
The common application of insert molding
Automobile
Automobile combine many small to large, simple to complex parts. In order to meet various needs such as cold resistance, heat resistance, impact resistance, and earthquake resistance, the materials used are also diverse. If they are shot one by one and then assembled, it will be very complicated. And time-consuming and labor-intensive. The advantage of embedded injection is that it can combine metal, rubber and plastic composite products to design devices such as sensors and gears.
〈Extension Reading:Why silicone rubber can be your best choice?〉
Daily use products
Composite products are everywhere in our life, whether it is scissors, extension cords, shoes... embedded and injected products can be seen everywhere. Most of the traditional bonding composite materials are simply combined by heating, pressurizing, etc., which is not only time-consuming and labor-intensive, but also difficult to maintain a certain level of quality and size, and the waste generated also increases the cost in disguise. Embedded and injected products have higher precision and tightness, greatly reduce waste and increase production efficiency. While reducing product costs, they also meet society's expectations for the price of daily necessities.
〈Extension Reading:What You Should Know About Silicone Rubber〉
Electronic Parts
Insert molding injection can provide a stable operating environment for electronic components. It is commonly used in more sensitive electronic panels and circuits embedded in impact-resistant, waterproof, and sun-resistant rubber and plastic materials to isolate external dust, water vapor, and affect electrical operations. ray wires. The demand for electronic parts is getting bigger and bigger. At the same time, many electronic parts are becoming more and more sophisticated. Insert molding injection is an injection technology that can quickly combine multiple components.
〈Extension Reading:What is silicone zebra connector and how they made?〉
Conclusion
The most attractive part of insert injection molding is the injection method that can effectively save a lot of time and money, and at the same time improve the fineness of the product. However, molds for insert injection require more considerations, so not all types of products are suitable for insert injection. It is necessary to discuss the best design process with professional manufacturers in order to produce the most competitive products. From the production of many parts to the finished product, in fact, there are not only the production methods of insert molding injection, but also die-cutting, thermoforming, or over-injection. It is the best choice for the foundry to have a variety of foundry processes. The one-stop advantage of Glory Sun Group is that we can provide you with suggestions on the best design method for each process, professional mold development experience, and the use of silicone raw materials from international manufacturers such as Shin-Etsu and Dowsil in the United States. The testing equipment and laboratory are also proficient in a variety of injection, embedded injection and other technologies, and they personally check everything from understanding the demand to delivery. 30 years of silicon rubber foundry and various technologies, passed ISO9001, ISO14001, IATF16949, ISO13485 certification affirmation, accumulated many years of foundry experience, can always provide you with the best quality solution, if you have a variety of injection OEM needs, welcome Contact us.
〈Extension Reading:Silicone Rubber OEM Manufacturers – Glory Sun Group〉
Article Classification
Recent Articles
- Applications of Liquid Silicone Rubber Injection Molding in smart clothing
- Discover the Versatility and Benefits of Liquid Silicone Rubber (LSR)
- The Application of Liquid Silicone Rubber in Seals and Gaskets
- Applications of Liquid Silicone Rubber in Medical Devices
- The Future of Liquid Silicone in Automotive Applications