BLOG
- Home
- Blog
- Liquid Silicone Rubber
- Applications of Liquid Silicone Rubber Injection Molding in smart clothing
Applications of Liquid Silicone Rubber Injection Molding in smart clothing
December 04,2024
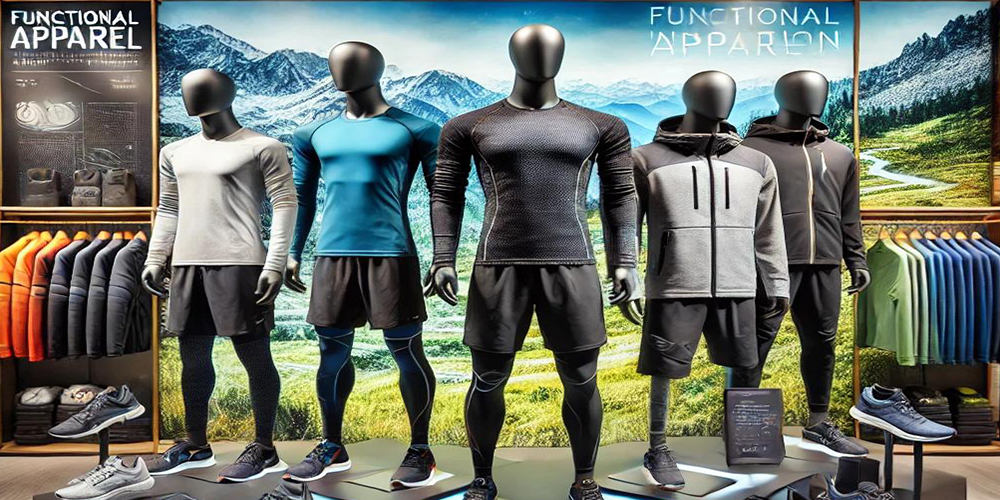
In the design and manufacturing of high-performance sports equipment, material selection is crucial. Liquid Silicone Rubber (LSR) is increasingly favored in the sports equipment industry due to its outstanding performance characteristics. This article will explore the applications of LSR injection molding technology in high-performance sports equipment and how it enhances the quality and functionality of these products.
What is Liquid Silicone Rubber Injection Molding?
Liquid Silicone Rubber (LSR) injection molding is an advanced processing technique that uses the flowability and high adhesion of liquid silicone to inject it into molds. After undergoing high-temperature curing, it forms precise silicone components. This technology enables the production of high-precision, complex silicone products with excellent durability and elasticity.
Advantages of Liquid Silicone Rubber in High-Performance Sports Equipment
Exceptional Comfort
Liquid silicone rubber offers excellent flexibility and comfort, making it an ideal material for high-performance sports equipment. For example, silicone knee pads and wrist guards provide superior comfort by reducing friction and discomfort during physical activities, thereby enhancing athletic performance.
High Durability and Weather Resistance
LSR can withstand extreme temperature changes and environmental conditions without losing its performance over time. This makes it highly suitable for use in high-intensity sports equipment, such as insoles and shock-absorbing pads for running shoes.
Excellent Anti-Slip Properties
The surface of liquid silicone rubber can be molded to have anti-slip textures, providing additional grip and stability. In sports shoes and other athletic gear, this feature significantly enhances user safety and performance.
Biocompatibility
Liquid silicone rubber is skin-friendly and does not cause allergic reactions or irritation. This is particularly important for sports equipment that comes into prolonged contact with the skin, such as protective gear.
Design Flexibility
LSR injection molding technology allows for the creation of complex and precise designs to meet various sports equipment needs. This flexibility enables designers to implement innovative designs that enhance the functionality and appearance of the equipment.
Application Examples of Liquid Silicone Rubber Injection Molding
Shoe Insoles
Liquid silicone rubber can be used to manufacture insoles for sports shoes, providing exceptional comfort and cushioning. These insoles not only enhance the durability of the shoes but also effectively reduce impact during physical activities.
Knee and Wrist Guards
High-performance silicone knee and wrist guards leverage the flexibility and elasticity of LSR to offer superior support and protection. These pieces of equipment can significantly reduce the risk of injuries and improve the wearer’s athletic capabilities.
Sports Protectors
LSR is also used to create other types of sports protectors, such as ankle and elbow guards. These protectors provide high levels of comfort and protection, making them essential gear for high-intensity sports.
Functional Apparel
The combination of liquid silicone rubber (LSR) injection molding with textile product is an innovative process that adds extra functionality and aesthetics to composite materials. This integration is effective in many applications, especially in high-performance sports equipment and other functional clothing. Below are the relevant steps and processes for combining LSR injection molding with knitted fabrics:
-
Step 1: Design and Mold Fabrication
Design Phase: First, determine how the liquid silicone rubber will integrate with the knitted fabric. Designers need to consider how the two materials will work together, such as using silicone as a localized reinforcement or as a full-covering functional layer. - Mold Fabrication: Specialized molds need to be created for injection molding. These molds must hold the fabric in place during the injection process and ensure that the silicone is evenly distributed across the fabric.
-
Step 2: Knitted Fabric Preparation
Fabric Selection: Choose the appropriate knitted fabric based on the final product's requirements. The choice of fabric affects the comfort, durability, and functionality of the final product. - Fabric Treatment: Sometimes, knitted fabrics need pre-treatment, such as cleaning or heating, to remove oils or impurities, thus enhancing the adhesion of silicone.
-
Step 3: Fabric Placement
Fabric Installation: Place the knitted fabric into the mold, typically using clamps or specialized fixtures to ensure the fabric's positioning during the injection process. This step is crucial as the fabric must remain stable while silicone is injected to ensure the quality of the final product. -
Step 4: Liquid Silicone Rubber Injection
Silicone Preparation: Prepare the liquid silicone rubber, adjusting its viscosity and flowability according to design requirements. LSR typically consists of two components that are mixed before injection. - Injection Molding: Inject the liquid silicone rubber into the mold, ensuring it completely covers the fabric. The pressure and temperature during the injection molding process must be precisely controlled to ensure a good bond between the silicone and the fabric.
-
Step 5: Curing and Cooling
Curing: After injection molding, the silicone needs to go through a curing process, which usually involves heating the mold in a curing oven to solidify the liquid silicone into a solid form. - Cooling: After curing, the mold and the product need to be cooled to safely remove the final product.
-
Step 6: Post-Processing
Mold Removal: Carefully remove the final product from the mold and inspect for any defects or areas needing adjustment. - Cleaning and Trimming: Perform necessary cleaning and trimming to remove excess silicone or fabric edges. This may include removing any overflow of silicone or trimming the fabric.
-
Step 7: Quality Inspection
Inspection and Testing: Conduct comprehensive quality checks on the final product, including verifying the bond between the silicone and fabric and testing the product's functionality and comfort. -
Step 8: Final Product Handling
Packaging: Package the final product for delivery to customers or market sale.
The integration of liquid silicone rubber injection molding with knitted fabrics provides innovative solutions for many high-performance sports equipment and functional products. Through precise processes and design, significant improvements in performance and comfort can be achieved.
Conclusion
The application of liquid silicone rubber injection molding technology in high-performance sports equipment highlights its advantages in terms of comfort, durability, anti-slip properties, and design flexibility. With ongoing advancements in technology, LSR is expected to play an increasingly important role in the sports equipment industry, offering higher performance and more comfortable gear for athletes. If you are interested in learning more about this technology or wish to apply it to your products, please feel free to contact us. We are happy to provide further expert advice and technical support.
Article Classification
Recent Articles
- Applications of Liquid Silicone Rubber Injection Molding in smart clothing
- Discover the Versatility and Benefits of Liquid Silicone Rubber (LSR)
- The Application of Liquid Silicone Rubber in Seals and Gaskets
- Applications of Liquid Silicone Rubber in Medical Devices
- The Future of Liquid Silicone in Automotive Applications