BLOG
- Home
- Blog
- Silicone Rubber Introduction
- Cultivating a Deeper Understanding of Silicone Hardness
Cultivating a Deeper Understanding of Silicone Hardness
September 26,2023
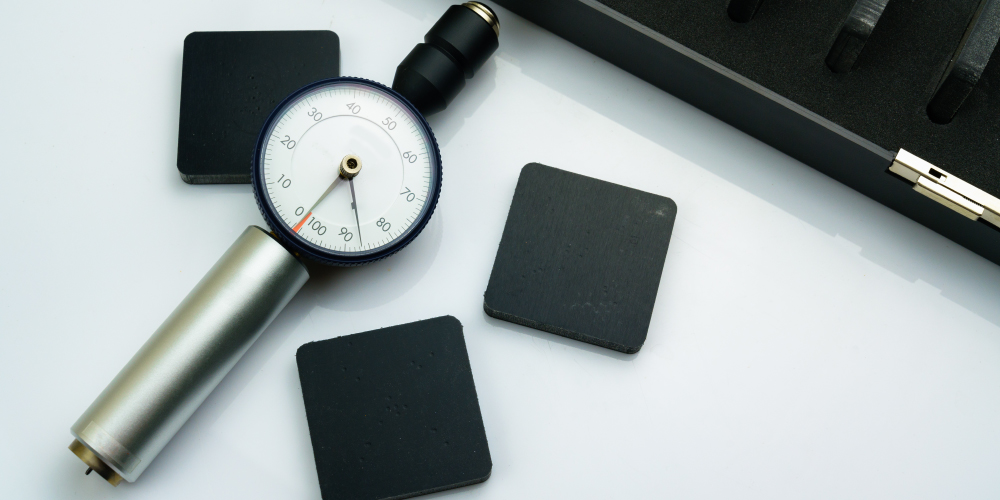
When developing silicone products, in addition to choosing the raw materials, injection techniques, and collaborating with manufacturing partners, silicone hardness is also a crucial consideration. Silicone hardness directly affects the performance of the final product. So, what are the factors that influence silicone hardness, and how is silicone hardness measured? We've compiled a quick guide to answer these common questions.
<Extension:What is the common elastomeric silicone? here is some tips you can't miss out>
Additionally, Shore hardness (Shore) testing is categorized into Type A and Type D. Testers choose between these types based on the hardness of the material being tested. Typically, Type A Shore hardness gauges are suitable for hardness values below 90 degrees, while Type D Shore hardness gauges are used for values above 90 degrees. The choice of which type to use is often determined by the tester's experience. Shore hardness gauges find application in a wide range of materials, including silicone, rubber, leather, plastic, resin, glass, acrylic, and more. This versatility makes them commonly used in industrial product testing.
<Extension:All Types and Applications of Silicone Injection Molding>
<Extension:What You Should Know About Silicone Rubber?>
<Extension:How is silicone rubber molded?>
4 Key Factors Affecting Silicone Hardness
The factors that influence silicone hardness mainly revolve around the formulation of raw materials during the product's uncured stage and the processing and molding phase. Below, we'll provide a detailed explanation of the key factors that affect silicone hardness:
Composition
Silicone is composed of natural silicon, oxygen, carbon, hydrogen, and other elements. To change the hardness of silicone, you need to control the chemical substances in the raw materials. Adjustments can be made by adding components like silicone resin, silicone oil, ethylene, and colloidal silica to the silicone raw materials. These additives can alter the chemical structure, crystallinity, and compatibility of silicone rubber, but it requires the expertise of professionals to control these details.<Extension:What is the common elastomeric silicone? here is some tips you can't miss out>
Curing Time
The molding process for silicone involves a curing or solidification phase. This can occur either at room temperature or through heating. By adjusting the curing time and temperature, you can change the hardness of silicone products.
Crosslinking Density
Crosslinking density refers to the tightness of the chemical bonds within silicone material. Imagine the chemical structure of silicone as a network, where intersecting points are created by different molecular chains. When these intersection points are closer together, the network becomes denser, resulting in harder silicone. The degree of crosslinking is influenced by factors such as heating temperature, heating time, and pressure during the manufacturing process.
Additives
Additives are used during the silicone molding process, especially during vulcanization. These additives stabilize the molecular structure, enhance hardness, and improve various properties of silicone. Additives come in various types, including fillers, vulcanizing agents, modifiers, and structure controllers. Adjusting the proportions of these additives can affect silicone hardness.
How to Measure Silicone Hardness
Silicone hardness is typically measured using a hardness tester. There are two common standards for measuring silicone hardness:
Shore Hardness
The Shore hardness gauge consists of a probe and a spring device. The testing procedure involves pressing the probe onto the test material, measuring the depth to which the probe is pressed under a specific spring force, and then converting this measurement into a hardness value. The principle behind this method is that when the probe is pressed into the surface of the material, the spring is compressed, generating a force that causes the probe to rebound. As the hardness of the tested silicone increases, the reactive force on the probe also increases, resulting in a higher Shore hardness reading.Additionally, Shore hardness (Shore) testing is categorized into Type A and Type D. Testers choose between these types based on the hardness of the material being tested. Typically, Type A Shore hardness gauges are suitable for hardness values below 90 degrees, while Type D Shore hardness gauges are used for values above 90 degrees. The choice of which type to use is often determined by the tester's experience. Shore hardness gauges find application in a wide range of materials, including silicone, rubber, leather, plastic, resin, glass, acrylic, and more. This versatility makes them commonly used in industrial product testing.
International Rubber Hardness Degrees (IRHD)
IRHD, also known as International Rubber Hardness Degrees, uses a different method involving a flat plane and a steel ball. The steel ball is pressed onto the test material from above, and the hardness value is determined based on the depth of indentation. IRHD has several categories, including Micro, Low, Normal, and Hard, each suited to specific types of materials.
Common Questions about Silicone Hardness
Q1: Is higher silicone hardness better?
Higher silicone hardness doesn't necessarily mean better. Extremely hard silicone can be less flexible and more prone to breakage. The choice of hardness should depend on the type and purpose of the product. Common silicone kitchenware, for example, typically falls in the range of Shore hardness 50A to 70A. The selection of hardness also affects the choice of production techniques and manufacturing costs.<Extension:All Types and Applications of Silicone Injection Molding>
Q2: Does environmental factors affect silicone hardness?
No, silicone is generally resistant to temperature variations, withstanding temperatures from -40°C to 200°C. Once silicone products are fully cured, their hardness is not significantly affected by environmental factors. However, prolonged exposure to sunlight, which includes UV radiation, may cause discoloration or aging of silicone products.<Extension:What You Should Know About Silicone Rubber?>
Q3: Does the molding method affect product hardness?
No, the choice of silicone molding method is primarily based on the type of product and budget considerations and does not directly influence the hardness of the final product. The key factors affecting silicone hardness are composition, curing time, and additives used during the manufacturing process.<Extension:How is silicone rubber molded?>
Q4: Does silicone hardness affect rebound and tensile strength?
Hardness may influence characteristics like elongation at break, tensile strength, rebound resilience, and permanent deformation under compression. Silicone material's physical properties, including hardness, elongation at break, tensile strength, etc., can be found in the material property sheet provided by manufacturers. For more detailed information on the physical properties of silicone materials, you can refer to these data sheets.- Hardness Shore A:The hardness of a product refers to its ability to resist the penetration of a hard object into its surface. When the hardness value is higher, it indicates that the product is harder.
- Elongation at break:The elongation at break is the percentage increase in length when a product stretches until it breaks, compared to its original length. When silicone is harder, the elongation at break tends to be lower.
- Tensile strength:The maximum strength value obtained when a product is continuously stretched until it breaks is known as tensile strength. Typically, silicone has a tensile strength of approximately less than 10 MPa, while heat-cured silicone's tensile strength generally falls in the range of 4.0 to 12.5 MPa.
- Tear strength:Under specific testing conditions, force is applied to an item with a cut to test its resistance to the expansion or tearing of the cut when subjected to external forces. This property is known as tear strength.
- Rebound resilience:The ability of a tested product to return to its original shape after undergoing temporary deformation due to external forces is referred to as resilience.
- Compression set:The probability of a product being subjected to external pressure under specific test conditions to the point where it cannot recover is tested. This is known as the permanent compression set test.
GSUN Silicone Rubber Physical Property table
Property | CHN-9300-U | CHN-9500-U | CHN-9600-U | CHN-9700-U | CHN-6300-U | CHN-6400-U | CHN-6500-U |
---|---|---|---|---|---|---|---|
Appearance | Translucent | Translucent | Translucent | Translucent | Translucent | Translucent | Translucent |
Density | 1.08 | 1.15 | 1.18 | 1.21 | 1.08 | 1.1 | 1.13 |
Hardness Shore A | 30 | 51 | 59 | 70 | 28 | 41 | 49 |
Elongation at break(%) | 640 | 390 | 370 | 200 | 690 | 530 | 540 |
Tensile strength Mpa | 5.4 | 8.7 | 8.8 | 8.5 | 7.4 | 8.2 | 10.8 |
Tear strength kN/m | 16 | 24 | 25 | 24 | / | / | / |
Rebound resilience (%) | 72 | 72 | 62 | 55 | 69 | 70 | 66 |
Compression set(%) | 10 | 7 | 9 | 7 | 14 | 12 | 13 |