BLOG
- Home
- Blog
- Liquid Silicone Rubber
- Liquid Injection Molding (LIM) VS Compression Molding; what fits you best?
Liquid Injection Molding (LIM) VS Compression Molding; what fits you best?
September 23,2021
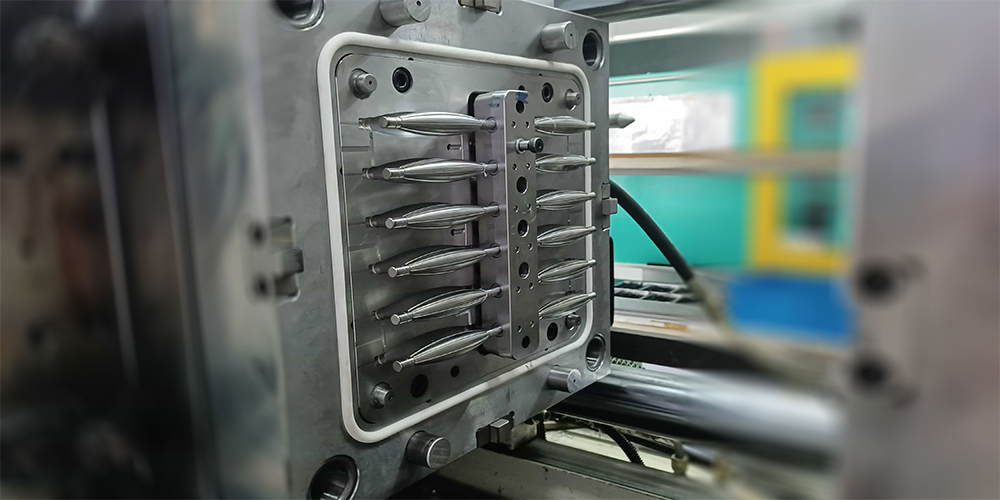
The selection between the liquid silicone rubber injection molding (LSR LIM) VS compression molding is always a dilemma for the customers, also a never-end argument among leading manufacturers, but who’s right? There are advantages and disadvantages to each molding process. Which technique reigns supreme?
What kinds of silicone products are suitable to be made by liquid silicone rubber injection molding (LSR LIM)?
Theoretically, most products that can be accomplished by compression molds can be produced by LIM molding, on the contrary, the compression molding couldn’t replace the LIM in some ways:
-
Appearance:
The parting line generally determines the quality of the product after molding. This is also the most obvious feature to judge the difference between the two (LIM & Compression Molding). During the LIM, The raw materials are fed after the molds are merged, and the curing process is completed at the high temperature of the molds. There’s no way to generate the burr, flash (parting line), the appearance is relatively good. The compression molding is the opposite. The raw materials are placed on the opened mold cavities first, and then the molds are closed and heated to solidify. The burrs or flash is generally inevitable. The parting line or burrs of molded silicone products are less than 0.25mm under general industry standards. However, the burrs of the parting line of LSR LIM products are almost zero.
The feeding method of the LIM is controlled by the microcomputer, which can accurately control the feeding weight of each mold, and the output product has high precision and tolerances can be minimized.
So, if you are chasing a high standard of appearance-looking and precise dimension function, you won’t want to miss out on the LIM solution. -
Efficiency:
The automation-oriented technology of LIM will give a longer mold life; because most of the compression molding processes are manual operations, the slab is also moved manually, the life of the mold is naturally decreased with the increase of production time (mold shot cycle), and the quality, accuracy of the products will become lower with the mold.
Shorter curing time; the molecular structure of liquid silicone products is different from solid silicone products. That makes its curing time under the suitable temperature is only one-third of that of solid silicone products, so the production cycle is greatly shortened and the production efficiency is greatly improved.
Although the molding speed of LIM is faster than compression molding, the LIM isn’t always the best solution considering the cost-performance ratio. For example like multi-color specification, gasket/O ring, and keypads with conductive pills have a low level of technical requirements and belongs to the matured industry which can be handled by the same old-matured procedures like compression molding. -
Quality/Lifespan:
The packaging of LSR raw materials is fully sealed. During the molding process, from feeding to forming, are all in a closed pipeline and film cavity. They will not contact the outside air at all, so the products will not be polluted by the external environment.
Absolutely environmental-friendly and non-toxic with high transparency of texture make LSR widely used in the high safety of the medical, cookware, and baby care products industry. These are all fragile and sensitive industries that can't be achieved by compression molding techniques. High-level transparency and pure like glass, which makes LSR become so popular at pacifiers, diving goggles, and suction nozzles.
High strength and high tear resistance of LSR are other features that (HCR/HTV) solid silicone rubber can't beat. General solid silicone rubber is very fragile and can be torn if it can’t withstand much tension. Even go through the reinforcement of pre-processes by the gas phase method is still not comparable to LSR. For example like LSR medical balloons, LSR cable ties, etc. are the representative products of this superiority.
LSR products are not much different from other solid silicone products in terms of lifespan. Because LSR is also part of silicone rubber, they share almost the same physical property with equal advantages and disadvantages.
More Advantage and Application of LSR LIM:
LSR required a lower molding temperature only needs to be 100-130 degrees while the molding temperature of solid silicone products is around 170 degrees. So compression molding cannot be used on silicone-coated plastic products or silicone rubber + Plastic composite products due to the plastic cannot withstand high temperatures under traditional compression molding.
Moreover, LSR has very good fluidity because of its liquid state, and it can fill the cavity without high injection pressure, so it is suitable for the molding of various thin-walled, narrow groove and long-tube shape structures of products.
The most classic products produced by LIM are LSR duckbill valves and LSR pacifiers. Both of these products are typical of mass production. Although the raw material cost of LSR is higher than that of solid silicone rubber (High-Temperature Vulcanization, HTV or High Consistency Rubber, HCR), there is no waste during the production process of liquid silicone. The overall cost is actually more economical. Plus, LSR pacifiers have higher standards of transparency requirements which are HTV or HCR that couldn’t compete.
Another special reason for specifying LSR LIM is that the product itself requires low compression and permanent deformation and high elasticity. Similarly, some LSR seals have the same requirements, so they are also produced by LSR LIM.
Some silicone products that are in direct contact with the human body will use LSR, such as face masks, laryngeal masks, medical supplies, and other products because they attach importance to the processing of the mold line to improve comfort. There are other products that are also processed by LIM, such as silicone cable accessories, silicone watch straps, silicone mobile phone cases, silicone baby bottles, silicone bowls, silicone nose pads, silicone earplugs, silicone diving glasses, various silicone tubes, and automotive accessories and so on.
In short, there are many liquid silicone products that can be injection molded.
Moreover, LSR has very good fluidity because of its liquid state, and it can fill the cavity without high injection pressure, so it is suitable for the molding of various thin-walled, narrow groove and long-tube shape structures of products.
The most classic products produced by LIM are LSR duckbill valves and LSR pacifiers. Both of these products are typical of mass production. Although the raw material cost of LSR is higher than that of solid silicone rubber (High-Temperature Vulcanization, HTV or High Consistency Rubber, HCR), there is no waste during the production process of liquid silicone. The overall cost is actually more economical. Plus, LSR pacifiers have higher standards of transparency requirements which are HTV or HCR that couldn’t compete.
Another special reason for specifying LSR LIM is that the product itself requires low compression and permanent deformation and high elasticity. Similarly, some LSR seals have the same requirements, so they are also produced by LSR LIM.
Some silicone products that are in direct contact with the human body will use LSR, such as face masks, laryngeal masks, medical supplies, and other products because they attach importance to the processing of the mold line to improve comfort. There are other products that are also processed by LIM, such as silicone cable accessories, silicone watch straps, silicone mobile phone cases, silicone baby bottles, silicone bowls, silicone nose pads, silicone earplugs, silicone diving glasses, various silicone tubes, and automotive accessories and so on.
In short, there are many liquid silicone products that can be injection molded.
Conclusion
So, the real question here isn’t WHICH will you choose, it’s WHY you choose it? Compression molding and injection molding each have their advantages and disadvantages, but who reigns supreme depends on what you’re producing.
An optimal choice of molding method under the various situation
GSUN specializes in liquid silicone rubber injection molding and understands crucial processing differences among injection, compression, transfer molding. We also offer the solutions for three of them.
Reach out, if you have a project that needs our expertise and supply chain solutions!
Article Classification
Recent Articles
- Applications of Liquid Silicone Rubber Injection Molding in smart clothing
- Discover the Versatility and Benefits of Liquid Silicone Rubber (LSR)
- The Application of Liquid Silicone Rubber in Seals and Gaskets
- Applications of Liquid Silicone Rubber in Medical Devices
- The Future of Liquid Silicone in Automotive Applications